Cu Seed Composition and Thickness
PCB panel
Introduction
Seed copper is deposited during the PCB manufacturing process, often over other Cu layers, a process that requires accuracy in the thickness of this thin layer. Measurement of the seed layer thickness for quality assurance is available using Energy Dispersive X-ray Fluorescence (EDXRF), which overcomes the challenge of differentiating seed copper from the Cu layer beneath.
XRF Analysis
- XRF results of sample surface
- The following elements were detected: Cu, Al, Si, S, Fe, Ni, Cu
- Further analysis examples:
- Light element detection
- What other elements should be expected?
Acquisition time: 30 sec
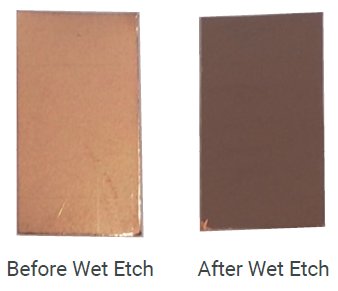
Wet etch
- Etch performed by dipping the sample (for one minute) in a solution containing:
- H₂0₂ (3%)
- Citric acid
- NaCl
Measurement objective
To measure the thickness of the top, electroless-deposited Cu seed layer at several sample locations.
Electroless Cu seeding (1 µm)
- ABF, Ajinmoto Build-up Film, is a carbon-based epoxy film developed by Ajinmoto Co.
- FR-4, flame retardant class 4, is a type of laminated substrate material used in the manufacture of printed circuit boards (PCBs).
Top Cu layer isolation
- The top Cu layer was removed from one of the samples using wet etch.
- XRF comparison was made between etch and non-etch samples.
- Cu Lα comes only from the top Cu layer.
Cu Lα saturation test
- For the top Cu layer, 1 µm is much below the saturation depth.
- Saturation in XRF is a specific depth of the layer whereby intensity no longer changes beyond this layer thickness.
- Thickness changes correlate to changes in the current.
- XRF measurement was performed at the same location using varying currents in order to determine the ideal linear section of the intensity vs. current curve.
Cu thickness sample comparison
- XRF scan was performed over six points (1 mm step) on three different samples.
- Cu Lα peak intensity was compared.
- The average intensity of Samples B and C were used as reference with thickness of 1 µm.
- Sample A has significantly thinner top Cu layer than Samples B and C.
- The top Cu layer of Samples B and C has uniform thickness, unlike Sample A.
Cu intensity
Intensity vs. current
Across-wafer variation
Cu layer thickness [µm]
Point | Sample A | Sample B | Sample C |
1 | 0.42 | 1.00 | 1.00 |
2 | 0.52 | 1.01 | 1.01 |
3 | 0.64 | 1.01 | 1.01 |
4 | 0.65 | 1.01 | 0.98 |
5 | 0.74 | 0.97 | 1.01 |
6 | 0.78 | 0.99 | 0.99 |
Average | 0.62 | 1.00 | 1.00 |
Cu seed thickness measurement by direct and indirect methods
- Cu layer thickness is measured by an automated algorithm using two methods.
- Direct method (0–0.7 µm) measuring the Cu Lα peak and calculating Cu layer thickness using linear regression
- Indirect method (0.7–1.4 µm) measuring the Si Kα peak and calculating Cu layer thickness using exponential regression
- Cu Lα peak intensity is saturated due to its low energy (0.93 keV), so the Cu layer thickness is measured indirectly using the Si from the ABF layer.
- Cu Lα and Si Lα were clearly detected by the EDXRF.
- Cu upper layer thickness can be monitored by using both peaks independently – Cu Lα or Si Kα peaks.
- Acquisition time: 12 sec
Nominal [µm] | Direct Method [µm] | Indirect Method [µm] |
0.4 | 0.398 | 0.382 |
0.5 | 0.496 | 0.462 |
0.6 | 0.613 | 0.571 |
0.7 | 0.689 | 0.704 |
0.8 | - | 0.788 |
0.9 | - | 0.888 |
1.0 | - | 0.960 |
1.1 | - | 1.083 |
Regression curves
- Linear regression for the direct method
- Exponential regression for the indirect method
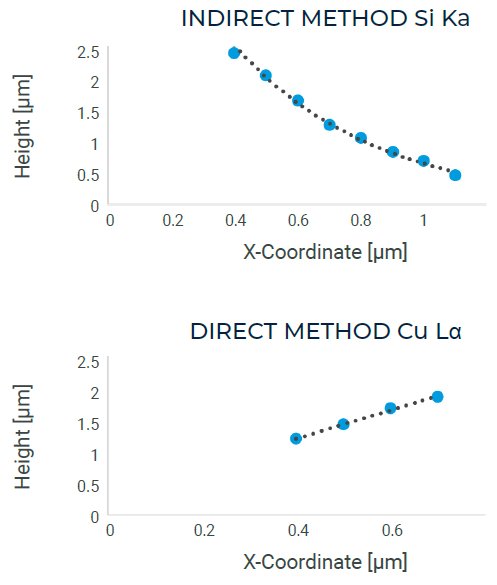
Roughness
- 3D scanner was used for measuring roughness by measuring surface height variations.
- Height variation up to 2 µm
3D scan imaging
2D microscope image
Summary
- XRF is very sensitive to thickness variation up to 0.1 nm. Many elements can be analyzed, qualitatively and quantitatively.
- Top Cu layer thickness can be measured using Cu Lα peak intensity changes.
- For accurate results, standards are required.
- The 3D scanner can monitor surface roughness.
Related products
ONYX 3000
EDXRF and optical hybrid metrology tool for automated X-ray analysis, 3D scanning, and 2D microscope for film thickness and composition measurements on blanket and patterned wafers for up to 300 mm wafers
Learn More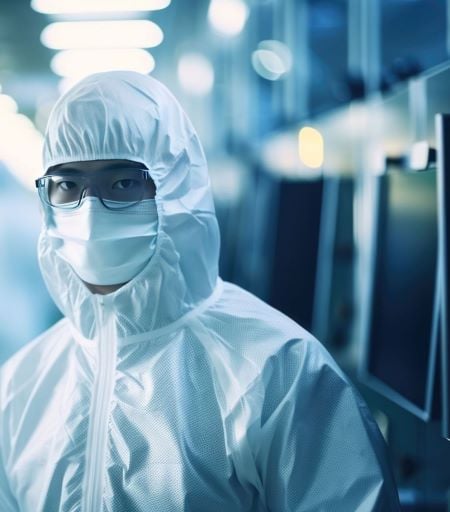
Contact Us
Whether you are interested in getting a quote, want a demo, need technical support, or simply have a question, we're here to help.