Single Wafer Pass Detection & Metrology
Introduction
In-line, single wafer pass capability to detect and analyze process issues provides a cost-effective method of implementing a hybrid metrology sensor capability.
The ONYX 3000 combines micro-spot X-ray and optical measurements to a address a wide variety of FEOL, BEOL, and advanced packaging applications.
Problem statement
Find a method of rapidly detecting and analyzing thin film issues on small area features, preferably in a single wafer pass. Typically, this task would involve in-line and off-line analysis tools and long measurement time which would interrupt the process flow, making it not feasible in a production environment.
Offered solution
The ONYX 3000 uses a highly-sensitive color 2D camera to qualitatively find evidence of a film issue on a feature, detecting an anomaly which can then be reviewed with an XRF measurement to rapidly quantify the issue.
UBM (Under Bump Metalization) defect detection and composition analysis
Objective
Detection of defective UBM (Under Bump Metalization) by full wafer scan with a 2D microscope using color image processing and further XRF analysis for elemental composition to monitor the process.
2D microscope defect detection
Image processing algorithms analyzed each frame to detect color defects. Reference color levels were set and gray level analysis was performed on each image; the following values were obtained:
(2D acquisition time 1 sec/frame)
XRF metrology
Suspected detected UBM defects are automatically delivered for XRF analysis of Au (Gold) thickness, monitoring Au variation with high sensitivity.
XRF analysis measurement presents a gap of 13% Au thickness in the dark-colored UBM. This finding matches the gray level results and demonstrates a significant process deviation.
(XRF acquisition time: 25 sec/site)
“Light” & “dark” colored pads: Detection, comparison, and material analysis
Objective
Identify defective pads by scanning a full wafer with the 2D microscope and analyzing those pads which deviate from a set gray level with EDXRF for elemental composition differences. Once pads were inspected and analyzed for gray levels, the XRF capabilities were applied to perform material analysis and to quantify the differentiation between the light pad and the dark pad.
2D microscope defect detection
Color differences were quantified by the image processing software. Different color pads were distinguished as “Light” and “Dark.” RGB values were analyzed.
(2D acquisition time 1 sec/site)
XRF metrology
Both layers thickness and composition were measured with a single XRF acquisition. Element compositions of: Au (L), Pd (L), Ni (K), Cu (K) were differentiated on the “Light” and “Dark” pads.
(XRF acquisition time: 10 sec/site)
Fluorine on pad analysis
Objective
Scan and detect unwanted residuals on bond pads (fluorine in this case) using a highly-sensitive 2D color camera followed by a light-element EDXRF analysis verification of suspected pads.
2D microscope
Large area sampling of pads on each wafer (1 sec/pad) which detects out-of-spec gray levels.
Light-element EDXRF
Detectors and helium purge of the air around the wafer are employed when revisiting suspect pads using a 20 μm diameter beam and analyzing for fluorine content.
XRF acquisition time: 14 sec / site
It can be seen from the XRF scans that the fluorine levels in the suspected pads are significantly higher than in the normal pads. The fluorine intensity level in the abnormal pad is 3.5X the level in the normal pad.
XRF can detect and quantify levels of fluorine in a specific pad. From the results below all pads contain various levels of fluorine. The pads with the higher level of fluorine (X3.5) can be detected using highly sensitive 2D imaging grey levels.
Using the hybrid sensor inspect and review method, scanning all pads on the wafer can be done in less than 4 minutes. Failure analysis will be performed by XRF. Any combination of 2D sampling and XRF threshold analysis is recipe driven.
Related products
ONYX 3000
EDXRF and optical hybrid metrology tool for automated X-ray analysis, 3D scanning, and 2D microscope for film thickness and composition measurements on blanket and patterned wafers for up to 300 mm wafers
Learn MoreONYX 3200
EDXRF and optical hybrid metrology tool for automated X-ray analysis, 3D scanning, and 2D microscope for film thickness and composition measurements on blanket and patterned wafers for up to 300 mm wafers
Learn More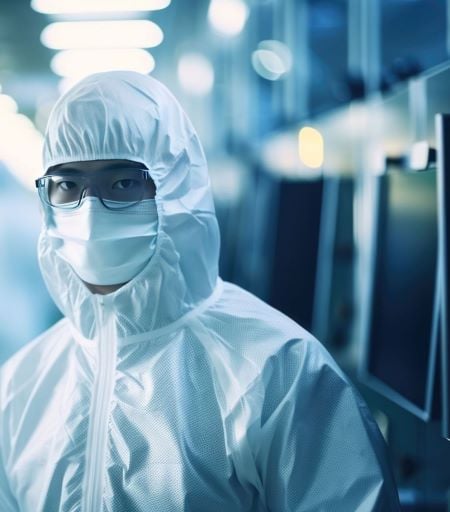
Contact Us
Whether you are interested in getting a quote, want a demo, need technical support, or simply have a question, we're here to help.