Fe, Ni and Co Based Alloy Analysis by Fundamental Parameter Method using ZSX Primus III+
Introduction
Fe, Ni and Co based alloys, including high-temperature alloys, tool steel, and stainless steel, have broad ranges of concentrations for many elements. These alloys are analyzed during production control by X-ray fluorescence (XRF) spectrometry. The calibration curves have to be separated into many groups when using the empirical calibration method even if matrix correction is introduced, because of strong inter-element absorption and enhancement effects. The basic theoretical formula of the fluorescent X-ray intensity for the Fundamental Parameter (FP) Method was established by Sherman(1) in 1955. Shiraiwa and Fujino(2) completed the formula by correcting for secondary excitation.
In 1983, Rigaku became the first XRF manufacturer to introduce FP method software for a wavelength dispersive (WD)XRF spectrometer, and the FP method has been widely used from screening analysis as semi-quantitative analysis to production control in many industries.
In this application note, quantitative analysis by the FP method for Fe, Ni and Co based alloys using the ZSX Primus III+ is demonstrated.
Instrument
The ZSX Primus III+, a tube-above sequential WDXRF spectrometer, is equipped with a 3 kW X-ray tube with a Rh target. WDXRF spectrometers give much better spectral resolution than energy-dispersive (ED) XRF spectrometers. Since Fe, Ni and Co based alloys contain many heavy elements, spectral resolution is essential. An optional analyzing crystal LiF(220), used in this note, adds more resolution to the WDXRF spectrometer.
Standard and sample preparation
Brammer Non-Destructive Reference Materials (20 samples) were used to establish the calibration. The concentration ranges of the calibration standards are shown in Table 1. The samples were polished with zirconia sandpaper #240.
Measurement
Measurements were performed using the ZSX Primus III+ with a 3 kW Rh target X-ray tube. The Kα lines were measured for all elements except for tungsten and tantalum, for which the Lβ1 lines were used. The total counting time was 10 minutes. A LiF(220) analyzing crystal and a scintillation counter (SC) were used for the heavy elements from Cr to W. For Ti and V, a LiF(200) crystal and SC were used. A PET crystal was used for Si and Al, and an optional Ge crystal was used to provide high resolution for the measurement of P and S. A gas-flow proportional counter was used for all light elements. In order to improve peak-to-background ratio, Al125, Ni40 and Ni400 primary beam filters were used for Cr to Cu, Se to W and Sn respectively.
Calibration
FP sensitivity calibration was established, where the calibration lines were made by a regression calculation with theoretical intensity calculated by the FP method from concentrations of the calibration standards and the measured intensities. The FP sensitivity calibration lines of Fe, Ni and Co are shown in Figure 1.
Figure 1: Representative FP calibration lines of Fe, Ni and Co.
For some elements, an overlap correction using theoretical intensities was applied ("Quantitative Theoretical Overlap Correction", an optional program for the ZSX Software). When there is an absorption edge between a correcting line and an overlapping line, the overlap correction does not work well because the intensity of the correction line is not proportional with the overlapping line. To avoid this situation, the theoretical intensity calculated taking into consideration absorption and enhancement by co-existing elements, is used for the overlap correction. In Table 1, the correction lines are shown.
Analysis results
Seventy-two samples of Brammer Non-Destructive Reference Materials, which do not include the samples used for the calibration, were quantified. The results are shown as accuracy in Table 1, which are calculated by the following formula:
$Accuracy = \sqrt{ \frac{\sum_i{(C_i-\hat{C}_i)^2}}{n-2} }$
$C_i$: calculated value of standard sample
$\hat{C}_i$: reference value of standard sample
n : number of standard samples.
Table 1: Calibration summary. (unit mass%)
Element | Calibration range | Correcting line for overlap | Accuracy |
Al | 0.006 – 3.07 | 0.068 | |
Si | 0.007 – 4.06 | 0.025 | |
P | 0.002 – 0.03 | Mo-Ll | 0.0029 |
S | 0.001 – 0.309 | Mo-Kα, Co-Kα*1) | 0.0027 |
Ti | 0.002 – 3.19 | 0.014 | |
V | 0.001 – 2.03 | Ti-Kβ1 | 0.014 |
Cr | 0.002 – 25.45 | V-Kβ1 | 0.17 |
Mn | 0.0015 – 15.09 | Cr-Kβ1 | 0.041 |
Fe | 0.02 – 99.9 | 0.25 | |
Co | 0.0014 – 49.4 | Fe-Kβ1 | 0.061 |
Ni | 0.04 – 99.6 | 0.23 | |
Cu | 0.001 – 32.09 | Ni-Kβ1 | 0.016 |
Se | – 0.19 | W-Lγ1 | - *2) |
Zr | 0.002 – 0.058 | Zr-Kα*1) | 0.0018 |
Nb | 0.001 – 5.19 | Mo-Kα | 0.011 |
Mo | 0.001 – 15.45 | 0.046 | |
Sn | 0.0007 – 0.014 | 0.0027 | |
Ta | 0.002 – 0.75 | W-Lα, Nb-Kβ2(2) | 0.012 |
W | 0.007 – 17.98 | 0.12 |
*1) Correction by measured intensities
*2) Cannot be calculated; one sample is available.
To demonstrate stability, repeatability tests (10 runs) were carried out by running BNRM 80E (stainless steel, Grade 303), BNRM 625 (Ni based alloy, Grade Inco625) and BNRM 162 (special alloy, Grade HANES556). The test results are shown in Table 2.
Table 2: Repeatability test results (n=10). (unit: mass%)
Sample: BNRM 80E, Stainless steel Grade 303 | ||||
Element | Certified value | Average | Standard deviation | R.S.D. |
Mn | 1.68 | 1.74 | 0.007 | 0.40% |
P | 0.030 | 0.022 | 0.001 | 3.2% |
S | 0.309 | 0.368 | 0.001 | 0.27% |
Si | 0.58 | 0.52 | 0.002 | 0.38% |
Cu | 0.36 | 0.35 | 0.003 | 0.86% |
Ni | 8.14 | 8.04 | 0.014 | 0.17% |
Cr | 17.21 | 17.35 | 0.014 | 0.08% |
Mo | 0.55 | 0.56 | 0.001 | 0.18% |
W | 0.07 | 0.07 | 0.003 | 4.3% |
Co | 0.16 | 0.12 | 0.001 | 0.83% |
V | 0.07 | 0.07 | 0.001 | 1.4% |
Nb | 0.01 | 0.01 | 0.0003 | 3.0% |
Sn | (0.01) | 0.01 | 0.001 | 10.0% |
Fe | (70.8) | 70.7 | 0.016 | 0.02% |
Sample: BNRM 625, Nickel alloy Grade Inco625 | ||||
Element | Certified value | Average | Standard deviation | R.S.D. |
Ni | 60.8 | 61.2 | 0.02 | 0.03% |
Cr | 21.70 | 21.38 | 0.015 | 0.07% |
Mo | 8.51 | 8.50 | 0.007 | 0.08% |
Co | 0.10 | 0.09 | 0.002 | 2.2% |
Al | 0.20 | 0.25 | 0.002 | 0.80% |
Ti | 0.30 | 0.28 | 0.001 | 0.36% |
Cu | 0.35 | 0.33 | 0.002 | 0.61% |
Fe | 4.19 | 4.14 | 0.004 | 0.10% |
Si | 0.29 | 0.25 | 0.002 | 0.80% |
Mn | 0.21 | 0.21 | 0.002 | 0.95% |
Nb | 3.35 | 3.33 | 0.004 | 0.12% |
Sample: BNRM 162, Special alloy Grade HANES556 | ||||
Element | Certified value | Average | Standard deviation | R.S.D. |
Fe | 31.2 | 31.0 | 0.02 | 0.06% |
Mn | 0.91 | 0.93 | 0.004 | 0.43% |
Si | 0.38 | 0.32 | 0.003 | 0.94% |
Ni | 21.80 | 21.97 | 0.010 | 0.05% |
Cr | 21.60 | 21.74 | 0.018 | 0.08% |
Mo | 2.83 | 2.91 | 0.003 | 0.10% |
W | 2.38 | 2.38 | 0.016 | 0.67% |
Co | 17.83 | 17.81 | 0.018 | 0.10% |
Cu | 0.02 | 0.02 | 0.001 | 5.0% |
Nb | 0.011 | 0.010 | 0.0004 | 4.0% |
Ti | 0.023 | 0.020 | 0.0005 | 2.5% |
Ta | 0.75 | 0.75 | 0.009 | 1.2% |
Conclusions
The conventional empirical calibration method requires many calibration groups for the analysis of Fe, Ni and Co based alloys. The Rigaku FP method has achieved accurate analysis for the alloys with a single calibration for each element, covering very wide ranges of concentrations, using the ZSX PrimusIII+. The FP method in the ZSX Program makes the analysis simple and easy without the considerable work of dividing calibration groups and preparing many standards.
"Quantitative Theoretical Overlap Correction", where theoretical intensities, instead of measured intensities, are used for overlap correction in quantitative analysis by the FP method, effectively works in the alloy analysis with many analysis elements and wide ranges of concentration.
Note) The analysis contents demonstrated in this application note can be provided using the Precalibration Package "FeCoNi Alloys", which is available for ZSX Primus IV, ZSX Primus III+ and ZSX Primus.
References
(1) J. Sherman: Spectrochem. Acta. 1,283 (1955)
(2) Shiraiwa and N. Fujino: Jpn. J. Appl. Phys. 5, 886 (1966)
Related products
ZSX Primus III NEXT
Affordable, high-end, tube-above Industrial WDXRF for the analysis of solid samples
Learn MoreZSX Primus IV
High power, tube above, sequential WDXRF spectrometer with new ZSX Guidance expert system software
Learn More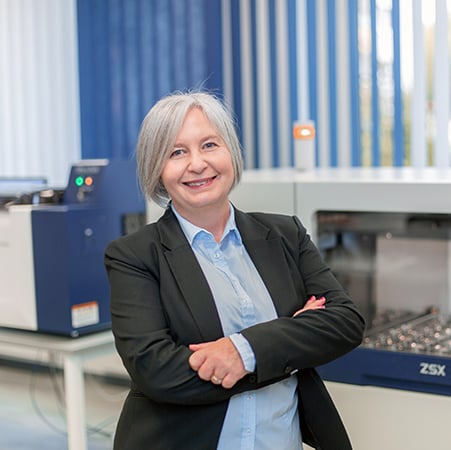
Contact Us
Whether you're interested in getting a quote, want a demo, need technical support, or simply have a question, we're here to help.