Dicing and Packaging
When analyzing a sample consisting of an extremely large number of micro-size parts, for example printed circuit boards, to help quantify the risk of failure it can be useful to evaluate the crystalline state of each part. To perform this analysis requires a focused X-ray beam small enough to illuminate single components and sufficient fine control of the sample position to identify and step through each position of interest. Earlier generation systems employed X-ray optics consisting of slits and collimators to cut down the divergent X-ray beam from the source into a small point beam on the sample. The downside of this inefficient approach is the large attenuation of the X-ray beam intensity and the resulting long data acquisition times. The present generation SmartLab μHR, a SmartLab model with microfocus source and advanced optics in combination with a high-speed 2D X-ray detector, can perform high contrast micro-area measurements in a substantially shorter amount of time than previous generation systems.
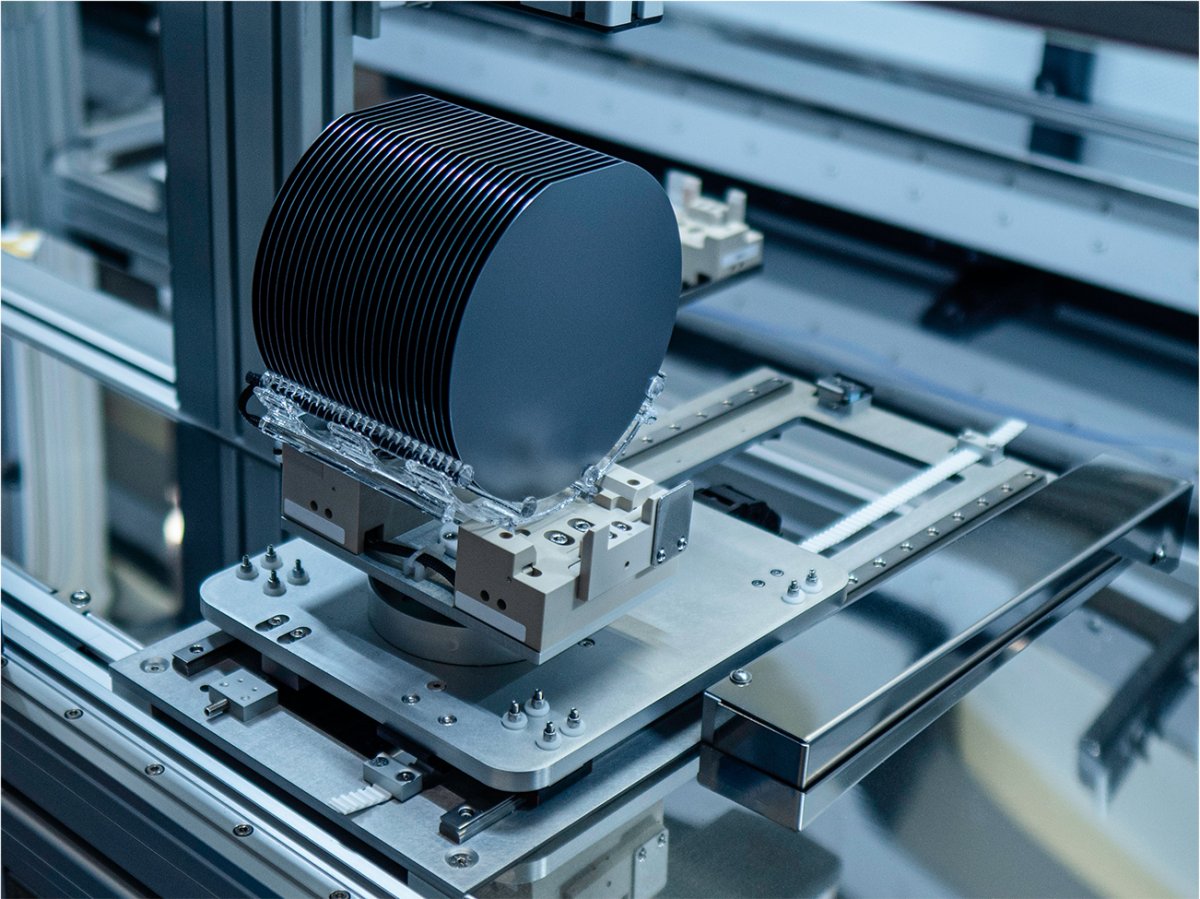
Mapping analysis
Qualitative analysis in the LED package
Consumer LED bulbs consist of multiple LED chips in a single bulb. When individual LED chips inside the bulb start to fail, the overall light intensity emitted by the bulb reduces. As the majority of LED chips used for light bulbs are several millimeter in size, an even smaller X-ray beam of about 100μm is required for the analysis the faulty part. The data below shows a point by point mapping around a failed LED element collected using a micro XRD system equipped with the micro-focusing X-ray optics and φ0.05 mm collimator. The use of multiple-point data mapping together with cluster analysis allows a comparison to be made between the different crystalline forms that occur at each analysis point within the LED chip.
Multiple-data mapping and cluster analysis
Data comparison of 2D XRD image between failed chip and normal chip
The figures below show a comparison between 2D-XRD results collected on a normal and failed LED chips using the same high performance micro diffraction optical system. The image obtained from the failed LED component was visually observed to be different than the normal component. The 2D-XRD data of the failed component detected the presence of textured and random crystalline components which were not observed in the normal component. Furthermore, the crystalline substrate and buffer layers exhibited a wider mosaic spread.
2D-XRD images of the normal and failure LED chips
Related products
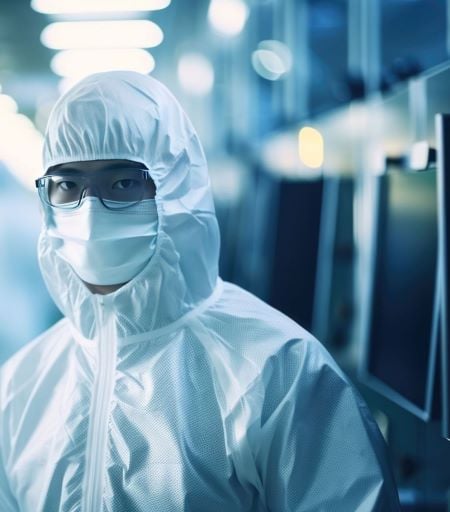
Contact Us
Whether you are interested in getting a quote, want a demo, need technical support, or simply have a question, we're here to help.