Quantification of Blast Furnace Slag by Rietveld Refinement using Reference Intensity Ratio
Introduction
In recent years, blended cement—cement into which additional constituents are mixed—has been widely produced with the aim of reducing environmental impact. According to JIS (Japanese Industrial Standard) R5211, blast furnace cement mixed with Blast Furnace Slag (BFS) is classified into three types according to the mixing ratio of BFS: Type A (from 5 to 30%), Type B (from 30 to 60%), and Type C (from 60 to 70%). Type B blast furnace cements mixed with 40–45% BFS are popular blast furnace cements. For quality control of blast furnace cement, quantitative analysis of BFS is normally performed by the Rietveld refinement combined with a standard material because BFS is an amorphous component. In this example, BFS in blast furnace cement was quantified by Rietveld refinement using the reference intensity ratio (RIR) without a standard material. The RIR value of the amorphous component was calculated from a simulated blast furnace cement with known content.
Measurements and results
BFS was added to Portland cement to prepare blast furnace cement samples. Each blast furnace cement sample with different mixing ratios of BFS was analyzed by a desktop X-ray diffractometer equipped with a high-speed 1D X-ray detector for 5 min. Figure 1 shows the result of Rietveld refinement of the blast furnace cement containing 40.0% of BFS. The quantitative analysis values of the blast furnace slag in each sample are shown in Table 1. The content of the amorphous component in the blast furnace cement was quantified within ±1% absolute error in the range of 40–45%. From these results, it is proved that this method is capable of performing accurate quantitative analysis.
Figure 1: Result of profile fitting of blast furnace cement by Rietveld refinement
Table 1: The quantitative values of the amorphous component in the blast furnace cements
Number | Sample 1 | Sample 2 | Sample 3 |
Preparation value (mass%) | 40.0 | 42.5 | 45.0 |
Quantitative value (mass%) | 40.3 | 42.2 | 45.4 |
Related products
MiniFlex
New sixth-generation general purpose benchtop XRD system for phase i.d and phase quantification
Learn MoreSmartLab
Advanced state-of-the-art high-resolution XRD system powered by Guidance expert system software
Learn MoreSmartLab SE
Highly versatile multipurpose X-ray diffractometer with built-in intelligent guidance
Learn More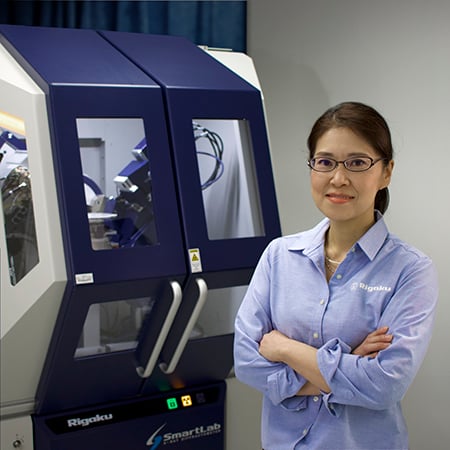
Contact Us
Whether you're interested in getting a quote, want a demo, need technical support, or simply have a question, we're here to help.