Quantitative Analysis of Blast Furnace Slag by Fusion Method
Introduction
Blast furnace slag is formed when iron ore or iron pellet, coke and flux are melted in a blast furnace of the iron foundry. The rapid chemical analysis of a blast furnace slag is an important task to control the blast furnace. X-ray fluorescence spectrometers are the most common analysis tools to analyze powder samples in iron and steel making process.
This application note describes blast furnace slag analysis using ZSX Primus III+.
Instrument
The ZSX Primus III+ has tube-above optics, where the X-ray tube is placed above the sample. Tube-above optics reduces the risk of instrument contamination or damage that can occur when pressed pellet samples break inside the spectrometer while being measured or transported to the measurement position. The ZSX Primus III+ is ideal for the steel industry where both bulk metal and powder samples are analyzed as part of the process control in steel manufacturing. The system software is based on Rigaku’s Flowbar interface that leads the user through a series of step by step procedures to optimize and execute measurements. “EZ analysis”, another Rigaku software innovation, greatly simplifies the analysis setup and sample analysis. In addition, the software has various kinds of statistical process control functions for the steel industry. The blast furnace slag is often analyzed by the pressed pellet method in XRF. However, fusion method preparing the powder to fused bead gives accurate results by removing the errors caused by grain size and heterogeneity effects and the method is a popular analysis technique for blast furnace slags.
Standards and sample preparation
The certified reference materials of blast furnace slag which were provided by NCS (China national analysis center), JSS (Japan), BRAMMAR (UK) and CSMU (Czech) were used to establish the calibration. The well-dried (2 hours at 105°C) samples were fused with flux of SPECTROFLUX® 100B (4LiBO2:1Li2B4O7) supplied from Johnson Matthey, oxidation reagent (V2O5) and samples in the ratio 10 : 1 : 1 = 4 g : 0.4 g : 0.4 g by using a fusion machine.
Measurement and calibration
Measurements were performed using the ZSX Primus III+ with a 3 kW Rh target X-ray tube. The Kα lines were measured for the elements with the counting time of 20 seconds and only Na is measured 40 seconds.
An LiF(200) analyzing crystal was used for all the heavy elements from K to Mn. A PET was used for Si and Al, and an optional Ge was used to provide high resolution for the measurement of P and S. A scintillation counter was used for all the heavy elements and a gas flow proportional counter was used for all the light elements. An RX25 was used for Mg and Na analysis.
The calibration curves obtained are shown in Figure 1 through Figure 11.
Figure 1: Calibration curve for SiO₂
Figure 2: Calibration curve for Al₂O₃
Figure 3: Calibration curve for CaO
Figure 4: Calibration curve for MgO
Figure 5: Calibration curve for Fe₂O₃
Figure 6: Calibration curve for SO₃
Figure 7: Calibration curve for TiO₂
Figure 8: Calibration curve for P₂O₅
Figure 9: Calibration curve for MnO
Figure 10: Calibration curve for K₂O
Figure 11: Calibration curve for Na₂O
Theoretical alphas obtained by the fundamental parameter method included in the software package were applied to all the calibrations to correct for absorption and enhancement effects.
Results
The accuracies of the calibration curves are listed in Table 1 and the repeatability test results (10 times) are listed in Table 2.
Table 1: Accuracy of calibration curves (unit: mass%)
Component | Concentration Range | Accuracy |
SiO₂ | 14.9 - 44.00 | 0.15 |
Al₂O₃ | 0.57-14.6 | 0.12 |
CaO | 31.2 - 51.9 | 0.34 |
MgO | 0.73 - 16.97 | 0.17 |
Fe₂O₃ | 0 - 19.12 | 0.10 |
SO₃ | 0 - 2.84 | 0.093 |
TiO₂ | 0.34 - 2.63 | 0.054 |
P₂O₅ | 0.00 - 0.80 | 0.003 |
MnO | 0.07 - 5.70 | 0.096 |
K₂O | 0.00 - 0.67 | 0.018 |
Na₂O | 0.023 - 0.35 | 0.027 |
Table 2: Result of repeatability ( unit : mass% )
Component | Certified value | Average | Std dev. | RSD% | Sample |
SiO₂ | 36.10 | 35.97 | 0.0384 | 0.10 | 13824 |
Al₂O₃ | 7.73 | 7.63 | 0.0206 | 0.27 | 13824 |
CaO | 39.33 | 38.96 | 0.0143 | 0.04 | 13824 |
MgO | 13.94 | 13.96 | 0.0277 | 0.20 | 13824 |
Fe₂O₃ | 1.015 | 1.032 | 0.0015 | 0.14 | 13824 |
SO₃ | 1.512 | 1.581 | 0.0050 | 0.32 | 13824 |
TiO₂ | 0.37 | 0.36 | 0.0044 | 1.22 | 13824 |
P₂O₅ | 0.026 | 0.0259 | 0.0015 | 5.88 | 13824 |
MnO | 0.10 | 0.113 | 0.0010 | 0.88 | 13824 |
K₂O | 0.59 | 0.57 | 0.0022 | 0.34 | 7-1-010 |
Na₂O | 0.18 | 0.16 | 0.0122 | 7.63 | 7-1-010 |
The accuracy is calculated by the following formula:
$Accuracy = \sqrt{ \frac{\sum_i{(C_i-\hat{C}_i)^2}}{n-m} }$
$C_i$: calculated value of standard sample
$\hat{C}_i$: reference value of standard sample
n : number of standard samples.
m: degree of freedom (linear 2, quad. 3)
Conclusions
The results show that high precision and accurate analysis of the components in blast furnace slag can rapidly be performed in fusion method using ZSX Primus III+. It is also possible to analyze the blast fur-nace slag by the pressed pellet method.
In addition, the ZSX Primus III+ can be applied to vari-ous kinds of materials such as iron and sintered ores, coke, limestone and pig iron for the process control in iron foundry.
Related products
ZSX Primus III NEXT
Affordable, high-end, tube-above Industrial WDXRF for the analysis of solid samples
Learn More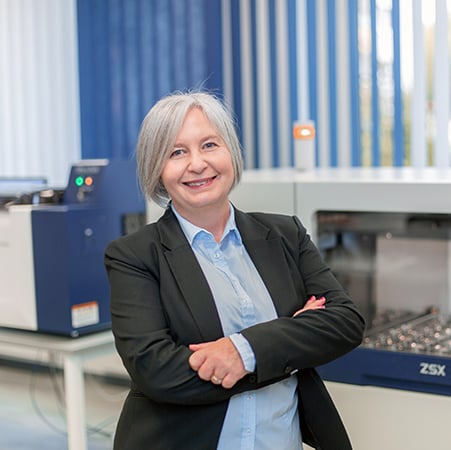
Contact Us
Whether you're interested in getting a quote, want a demo, need technical support, or simply have a question, we're here to help.