Fast Analysis of Mineralogical Phases in Blended Cements using Miniflex XpC
Introduction
Blended cements are becoming more popular to reduce CO₂ emissions and fuel consumption. They are produced by replacing clinker with additives like fly ash, pozzolan, or slag and substituting some fuel with waste materials such as RDF, used tires, elephant grass, and nut shells. These additives have similar or superior cement properties to traditional Portland cement but have a more complex mineralogical composition.
The mineralogical composition of blended cement is crucial in determining the finished product’s properties and, therefore, needs to be thoroughly analyzed and controlled. Rigaku’s MiniFlex XpC and EasyX software provide a fast and reliable solution for analyzing raw materials, additives, and finished cement products. The MiniFlex XpC is a robust, dependable X-ray diffractometer suitable for cement applications. It can be easily integrated into an automated lab using a conveyor belt or robot interface. The MiniFlex XpC has a small footprint and requires minimal infrastructure support, including external cooling water.
This application note presents typical results obtained while analyzing the mineralogical phases of blended cement, demonstrating the effectiveness of Rigaku’s MiniFlex XpC and EasyX software in providing accurate and comprehensive analysis.
Cement solutions
Rigaku’s MiniFlex XpC cement solution package is perfectly designed for fast measurements and easy phase quantifications. The analyzer is equipped with an 800 W tube, the D/teX Ultra250 high-speed 1D detector, and the EasyX software. MiniFlex XpC allows fast and precise measurement for the evaluation of all types of cement-related materials, such as clinker, slag, fly ash, blended cement, etc.
Measurement and phase quantification are performed in a three-step procedure; the industrial operator can set up measurement and analysis routines, which take less than three minutes.
Application specific
For this application note, two cement samples were analyzed using MiniFlex XpC. Figures 1 and 2 show the Rietveld refinements of a blast furnace slag cement (Each standard name: JIS R 5211, CEM III, ASTM Type IS) and a ternary blended cement (JIS R 5213, CEM III, ASTM Type IT) containing two amorphous phases (blast furnace slag and fly ash). The cement samples contain the typical clinker phases such as alite (M1 & M3 polymorphs), belite (α, α’, β), aluminate, and ferrite. The cement analysis quantification also yields additional phases, such as gypsum and bassanite.
Tables 1 and 2 are the quantification results of amorphous phases in blast furnace slag cement (Portland slag cement) and ternary blended cement in addition to crystalline phases. Quantification results of the amorphous phases of both samples were shown to be in good agreement with their known corresponding preparation value.
Summary
MiniFlex XpC and EasyX allow fast analysis of mineralogical phases in blended cements using Rietveld software simplified/automated for use in cement plants. The examples show the MiniFlex XpC is a perfect tool for quality & process control in a plant.
Figure 1: Rietveld refinement result of blast furnace slag cement. [Rwp: Weighted profile parameter S: Goodness of fit]
Figure 2: Rietveld refinement result of ternary blended cement.
Table 1: Quantitative result and static repetition values for blast furnace slag cement (mass%).
Components | Concentration (n=10) |
Standard deviation 1σ, n=10 (3σ) |
Alite-M3 (C₃S) | 25.0 | 0.2 (0.6) |
Alite-M1 (C₃S) | 11.3 | 0.2 (0.6) |
Total Alite | 36.4 | 0.2 (0.6) |
Belite-β (C₂S) | 6.8 | 0.2 (0.6) |
Belite-α’ (C₂S) | 1.2 | 0.1 (0.3) |
Total Belite | 8.0 | 0.2 (0.6) |
Aluminate-Cubic (C₃A) | 1.4 | 0.1 (0.3) |
Aluminate-Ortho (C₃A) | 1.8 | 0.1 (0.3) |
Total Aluminate | 3.2 | 0.2 (0.6) |
Ferrite (C₄AF) | 5.1 | 0.1 (0.3) |
Lime (CaO) | 0 | 0 |
Portlandite (Ca(OH)₂) | 0 | 0 |
Gypsum (CaSO₄(H₂O)₂) | 0.5 | 0.1 (0.3) |
Bassanite (CaSO₄(H₂O)₀.₅) | 1.2 | 0.1 (0.3) |
Anhydrite (CaSO₄) | 0 | 0 |
Periclase (MgO) | 0 | 0 |
Calcite (CaCO₃) | 0 | 0 |
Langbeinite (K₂Mg₂(SO₄)₃) | 0.3 | 0.1 (0.3) |
Blast furnace slag* | 45.2 | 0.2 (0.6) |
* Amount of BFS added: 45.0 mass%
Table 2: Quantitative result and static repetition values for ternary blended cement (mass%).
Components | Concentration (n=10) |
Standard deviation 1σ, n=10 (3σ) |
Alite-M3 (C₃S) | 20.8 | 0.1 (0.3) |
Alite-M1 (C₃S) | 7.8 | 0.2 (0.6) |
Total Alite | 28.6 | 0.2 (0.6) |
Belite-β (C₂S) | 5.8 | 0.2 (0.6) |
Belite-α’ (C₂S) | 0.2 | 0.1 (0.3) |
Total Belite | 6.0 | 0.2 (0.6) |
Aluminate-Cubic (C₃A) | 1.4 | 0.1 (0.3) |
Aluminate-Ortho (C₃A) | 1.9 | 0.1 (0.3) |
Total Aluminate | 3.3 | 0.2 (0.6) |
Ferrite (C₄AF) | 4.2 | 0.1 (0.3) |
Lime (CaO) | 0 | 0 |
Portlandite (COH₂) | 0 | 0 |
Gypsum (CaSO₄(H₂O)₂) | 1.1 | 0.1 (0.3) |
Bassanite (CaSO₄(H₂O)₀.₅) | 0.8 | 0.1 (0.3) |
Anhyrdrite (CaSO₄) | 0 | 0 |
Periclase (MgO) | 0 | 0 |
Calcite (CaCO₃) | 0.7 | 0.1 (3) |
Arcanite (K₂SO₄) | 0 | 0 |
Aphthitalite (K₃Na(SO₄)₂) | 0 | 0 |
Langbeinite (K₂Mg₂(SO₄)₃) | 0 | 0 |
Blast furnace slag* | 40.0 | 0.2 (0.6) |
Fly ash** (Amorphous, Quartz (SiO₂) and Mullite (Al₂.₄Si₀.₆O₄.₈)) | 15.1 | 0.2 (0.6) |
* Amount of BFS added: 40.0 mass%
** Amount of fly ash added: 15.0 mass%
Related products
MiniFlex XpC
Compact X-ray diffractometer for quality control of materials that is easy to use and is ideal for routine work
Learn More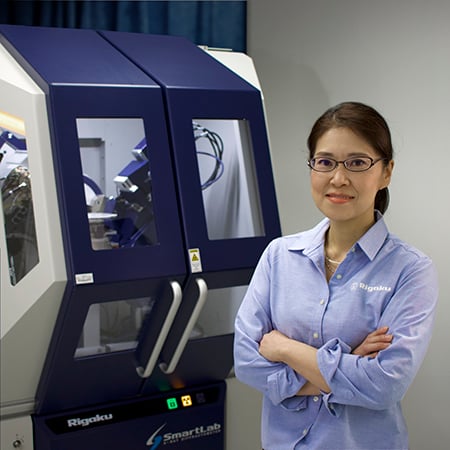
Contact Us
Whether you're interested in getting a quote, want a demo, need technical support, or simply have a question, we're here to help.