Quantitative Analysis of Stainless Steel using the ZSX Primus III NEXT
Introduction
Alloy steel with chromium of alloying element added is called stainless steel. Its advantage is not to rust or corrode as easily as ordinary steel. There are over 150 grades of stainless steel, which have many applications such as cookware and major appliances. Alloy steels are generally produced using electric furnaces. The concentrations of elements in molten steel are controlled in the process of steel making, therefore rapid and accurate analysis of elemental compositions are required. As part of the control of the steel making process, analyses of slag and raw materials such as quicklime and ferroalloys are also required. X-ray fluorescence spectrometers are the most common analysis tools to analyze steel owing to rapid analysis and the ability to measure both bulk metal and powders.
This application note describes stainless steel analysis using the ZSX Primus III NEXT, which is optimized for process control.
Instrument
The ZSX Primus III NEXT has tube above optics, where the X-ray tube is placed above the sample, Tube above optics reduce the risk of instrument contamination or damage that can occur when pressed pellet samples break inside the spectrometer while being measured or transported to the measurement position. The ZSX Primus III NEXT is ideal for the steel industry where both bulk metals and powder samples are analyzed as part of the process control protocol during the manufacture of alloy steels. The system software is based on Rigaku’s Flowbar interface that leads the user through a series of step by step procedure to optimize and execute measurements. “EZ analysis”, another Rigaku software innovation greatly simplifies the analysis setup and sample measurement. In addition, the software has various kinds of statistical process control functions ideal for the steel industry.
Standard and sample preparation
The certified standard reference materials of stainless steel provided by JSS (Japanese Iron and Steel Certified Reference Materials) were used to establish the calibration. The samples were polished with fine corundum abrasive paper with 240-grit for accurate analysis of Cr and Ni. The smooth surface is essential to obtain good results about these elements.
Measurement and calibration method
Measurements were performed using the ZSX Primus III NEXT with a 3 kW Rh target X-ray tube. The Kα line was measured for all the elements at a counting time of 20 seconds.
A LiF(200) analyzing crystal and scintillation counter were used for all the heavy elements from Cr to Mo. A PET crystal was used for Si and Al, and an optional Ge crystal was used to provide high resolution for the measurement of P and S.
A flow proportional counter was used for all the light elements.
The representative calibration curves obtained are shown in Figure 1 through Figure 10.
Figure 1: Calibration curve of Si
Figure 2: Calibration curve of Mn
Figure 3: Calibration curve of P
Figure 4: Calibration curve of S
Figure 5: Calibration curve of Ni
Figure 6: Calibration curve of Cr
Figure 7: Calibration curve of Mo
Figure 8: Calibration curve of Cu
Figure 9: Calibration curve of Co
Figure 10: Calibration curve of Nb
Theoretical alphas obtained in the software using the fundamental parameter method are applied to all the calibrations to correct absorption and enhancement effects. Overlapping correction was performed in the calibration of P and S for the overlapping of Mo and in the calibration of Co for the overlapping of Fe as shown in Figures 3, 4 and 9. As shown in the Figure 5 and 6, the good accuracy was obtained in the calibration curves of Ni and Cr.
Table 1: Accuracy of calibration curves (unit : mass%)
Component | Concentration range | Accuracy |
Si | 0.30 – 0.67 | 0.0073 |
Mn | 0.48 – 1.81 | 0.012 |
P | 0.023 – 0.035 | 0.00069 |
S | 0.0006 – 0.0185 | 0.0004 |
Ni | 0.18 – 19.42 | 0.062 |
Cr | 16.56 – 24.79 | 0.061 |
Mo | 0.013 – 2.13 | 0.0065 |
Cu | 0.020 – 0.39 | 0.007 |
Co | 0.013 – 0.26 | 0.0021 |
Nb | 0 – 0.55 | 0.0017 |
Table 2: Result of repeatability JSS655-11 (unit : mass%)
Component | Certified value | Average | Std dev. | RSD% |
Si | 0.67 | 0.67 | 0.0017 | 0.25 |
Mn | 1.77 | 1.77 | 0.0017 | 0.094 |
P | 0.028 | 0.028 | 0.00017 | 0.58 |
S | 0.0056 | 0.0072 | 0.00010 | 1.4 |
Ni | 9.41 | 9.39 | 0.0067 | 0.071 |
Cr | 17.47 | 17.50 | 0.0082 | 0.047 |
Mo | 0.096 | 0.103 | 0.00048 | 0.47 |
Cu | 0.12 | 0.12 | 0.00070 | 0.58 |
Co | 0.21 | 0.21 | 0.00053 | 0.25 |
Nb | 0.54 | 0.54 | 0.00045 | 0.083 |
Results
The accuracy of the calibration curves is listed in Table 1 and the repeatability of the test results (10 times) are shown in Table 2.
The accuracy is calculated by the following formula:
$Accuracy = \sqrt{ \frac{\sum_i{(C_i-\hat{C}_i)^2}}{n-m} }$
$C_i$: calculated value of standard sample
$\hat{C}_i$: reference value of standard sample
n : number of standard samples.
m: degree of freedom (linear 2, quad. 3)
Conclusions
The results demonstrate that high precision and accurate analysis of the elements in stainless steel, especially for Ni and Cr, can be performed using the ZSX Primus III NEXT. It is also possible to analyze low alloy steel and other high alloy steels. In addition, powder slag and powder raw materials such as quicklime and ferroalloys can also be analyzed with good precision using the ZSX Primus III NEXT, which is one of the best X-ray fluorescence spectrometer for process control of stainless steel plants.
Related products
ZSX Primus III NEXT
Affordable, high-end, tube-above Industrial WDXRF for the analysis of solid samples
Learn More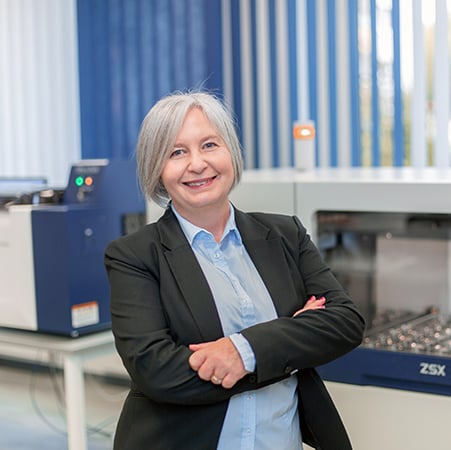
Contact Us
Whether you're interested in getting a quote, want a demo, need technical support, or simply have a question, we're here to help.