Quality and Process Control Analysis of Natural and Processed Iron Ores by the Pressed Powder Method
Introduction
Iron ore is the most abundant mineral resources and is also one of the most important materials in modern industries. Since the amount and cost of seaborne trade have increased in recent years, analytical requirements are becoming more stringent. Total iron (T.Fe) concentration in iron ore is a focal point for trade. Therefore, analysis to determine total iron requires high accuracy.
At the mining site, laboratory analysis covers quality control for Run-of-Mine and products, grade check for beneficiation and blending, and also research for area exploration. Similarly, iron ore analysis is required in pelletizing plants near mining sites and sintering plants, and stockyards in steel manufacturing sites. Wet chemical analysis, the traditional analytical technique for total iron determination, requires analytical skill and is time-consuming. There is high demand for analysis with cost-efficient parameters, such as speed of analysis, simplicity and accuracy.
For powder samples in X-ray fluorescence spectrometry, the pressed powder method is the best solution in terms of speed and simplicity. Since iron ore has complex matrices owing to varied mineral composition, appropriate corrections for these matrix effects are required in XRF analysis. The conventional correction technique for total iron is a method using Compton scattering as an internal standard (the Compton scattering ratio method) but it has not been rigorous enough to meet the requirements of the iron ore industry. Rigaku has developed an improved Compton scattering method by integrating theoretical alpha corrections to significantly improve analytical results.
This note demonstrates an improved method to determine total iron in natural and processed iron ores by the pressed powder method.
Instrument
The ZSX Primus III NEXT is a floor-standing sequential wavelength dispersive X-ray fluorescence (WDXRF) spectrometer, which has advantages of high spectral resolution and high sensitivity for light elements. The instrument is designed to provide reliable production control and flexibility for a wide range of applications. The ZSX Primus III NEXT is equipped with a 3 kW Rh target X-ray tube and three analyzing crystals covering from oxygen to uranium. Additional analyzing crystals are also available for boron to nitrogen analysis.
It has an intelligent auto sample changer (ASC), which is upgradable to 48 samples if needed.
The ZSX Primus III NEXT is optimized for powder sample analysis by adopting tube-above optics. This minimizes contamination from sample breaks during powder sample measurements. The tube-above optics also enable users to make pellets without any binding agents or with less binding agent than usual. This simplifies sample preparation and reduces labor hours, and is cost-effective since it reduces binding agent usage. A powder trap attachment is used to improve and minimize vacuum issues caused by loose particles from powder samples. The ZSX Primus III NEXT is also more resistant to dusty environment by adopting an enhanced housing.
Ease of use of the control software has been improved. The flowbar operation used to set-up quantitative analysis fully supports non-technical users.
“Quant Scatter FP” is a unique function integrated into the Rigaku FP system. It is possible to generate theoretical alphas in the internal standard method by using X-rays applied to heavy element analysis in some ores.
Standard and sample preparation
The standard samples used for calibration were 24 commercially available certified reference materials (CRMs). These standards are composed of hematite, magnetite, limonite, iron sand, sinter, pellet and pure iron oxide. The range of total iron concentration in these CRMs is wide from 29.0 to 71.1 in mass%.
The well-dried (2 hours at 105 °C) samples were ground in a tungsten carbide container and then pressed without any binder under a pressure of 250 kN using a sample cup. Generally, binders affect the analysis results in methods that use scattering X-rays as the internal standard. Therefore, it is strongly recommended to press samples such applications require high accuracy. When it is necessary to use pellets, binder should be added in low proportion. This note shows test results of a comparison between pelletizing with and without binder (see Results).
Measurement and calibration
The ZSX Primus III NEXT with a 3 kW Rh target X-ray tube was used to measure the Compton scattering lines (peak intensity only) and elemental lines of Fe, Si, Al, P, Mg, S, Ca, K, Ti, Mn and V. For the Fe-Kα measurement, an attenuator was used to obtain appropriate intensity without changing tube power. The optional Ge analyzing crystal was used for phosphorus and sulfur measurements. Count time for each element line was 40 s except for Fe which was 20 s.
The calibration equation for “total iron” is as follows:
$W_{Fe} = (AI_R + BI_R + C) ⋅ (1+ ∑α_jW_j )$
$I_R = I_{Fe}/I_{Compton}$
$α_j$: theoretical alpha of element j
$W_j$: weight fraction of element j
$I_{Fe}$: intensity of Fe-Kα line
$I_{Compton}$: intensity of Rh-Kα Compton line
Matrix correction coefficients (alphas) applied to the matrix correction in the calibrations were theoretically calculated using built-in FP software. The theoretical alphas for total iron calibration were calculated taking into consideration the Compton scattering ratio by the Quant Scattering FP function integrated in the FP software.
Results
The accuracy of the total iron calibration without using binder obtained in this study is excellent as shown in Figure 1.
Figure 1. Calibration curve of total iron (T.Fe) using the Compton scattering ratio with theoretical alpha correction (no binder sample)—open circle: uncorrected points ; filled diamond: corrected points
Table 1. Accuracy and binder condition
Binder | Mixture proportion to sample | Accuracy of calibration in Total Fe (mass%) |
Polymer | 11% | 0.20 |
Organic compound | 11% | 0.17 |
Inorganic compound | 11% | 0.19 |
Saccharide | 2.5% | 0.09 |
None | 0% | 0.10 |
Note the difference in accuracy between the tests with high binder content and others. The same six iron ore CRMs were used for each test.
Table 2. Accuracy of the calibration curves. Unit: mass%
Component/Element | Concentration range | Accuracy |
Total Fe | 29.0 - 71.1 | 0.14 |
SiO₂ | 1.7-45 | 0.69 |
CaO | 0.039-20 | 0.11 |
Mn | 0.018-1.1 | 0.0044 |
Al₂O₃ | 0.38-6.8 | 0.27 |
TiO₂ | 0.044-6.3 | 0.0078 |
MgO | 0.018-3.5 | 0.10 |
P | 0.014-0.59 | 0.0065 |
S | 0.002-0.85 | 0.0068 |
K₂O | 0.007-0.69 | 0.0067 |
V | 0.004-0.46 | 0.0020 |
Table 3. Analysis result of pellet ore. unit: mass%
Component / Element | Certified Value | duplicate 1 | duplicate 2 | ||
XRF | Diff. | XRF | Diff. | ||
Total Fe | 65.41 | 65.484 | 0.074 | 65.460 | 0.050 |
SiO₂ | 2.29 | 2.414 | .124 | 2.405 | 0.115 |
CaO | 2.49 | 2.610 | 0.120 | 2.610 | 0.120 |
Mn | 0.039 | 0.040 | 0.001 | 0.040 | 0.001 |
Al₂O₃ | 0.54 | 0.539 | 0.001 | 0.547 | 0.007 |
TiO₂ | 0.14 | 0.143 | 0.003 | 0.142 | 0.002 |
MgO | 0.49 | 0.489 | 0.001 | 0.489 | 0.001 |
P | 0.043 | 0.044 | 0.001 | 0.044 | 0.001 |
S | 0.003 | 0.003 | 0.000 | 0.003 | 0.000 |
K₂O | 0.098 | 0.094 | 0.004 | 0.094 | 0.004 |
V | 0.19 | 0.186 | 0.004 | 0.192 | 0.002 |
Table 4. Analysis result of sintered ore
Component / Element | Certified Value | duplicate 1 | duplicate 2 | ||
XRF | Diff. | XRF | Diff. | ||
Total Fe | 56.16 | 56.062 | 0.098 | 56.156 | 0.004 |
SiO₂ | 5.41 | 5.232 | 0.178 | 5.237 | 0.173 |
CaO | 9.91 | 9.860 | 0.050 | 9.886 | 0.024 |
Mn | 0.263 | 0.263 | 0.000 | 0.265 | 0.002 |
Al₂O₃ | 2.01 | 1.821 | 0.189 | 1.831 | 0.179 |
TiO₂ | 0.31 | 0.318 | 0.008 | 0.318 | 0.008 |
MgO | 1.62 | 1.688 | 0.068 | 1.699 | 0.079 |
P | 0.06 | 0.056 | 0.004 | 0.057 | 0.003 |
S | 0.012 | 0.012 | 0.000 | 0.012 | 0.000 |
K₂O | 0.036 | 0.037 | 0.001 | 0.037 | 0.001 |
V | 0.031 | 0.038 | 0.007 | 0.038 | 0.007 |
Table 1 shows the calibration accuracy of the binderless pellet and a pellet with low content binder (saccharide 2.5%) is comparable. On the other hand, accuracies of pressed pellets using binders with the usual mixing ratio (11%) shows 0.17 – 0.20 mass%. This indicates that, for the Compton scattering ratio method, it is necessary to minimize binder usage.
Calibration accuracies for all components measured in this study are listed in Table 2.
The accuracy is calculated by the following formula:
\begin{equation} \nonumber Accuracy = \sqrt{\frac{\sum_{i}(C_i-\hat{C_i})^2}{n-m}}\end{equation}
Ci: calculated value of standard sample
Ĉi: reference value of standard sample
n : number of standard samples.
m: degree of freedom (linear 2, quad. 3)
To evaluate this correction method, two types of processed iron ores in CRMs were analyzed. Measurements were performed for duplicated pressed pellet samples. The results are shown in Table 3 and 4.
Conclusions
X-ray fluorescence spectrometry is a rapid, precise and accurate method to meet the requirements of the iron ore industry. It can also minimize cost and time in iron ore analysis.
This application note demonstrated that this method is practically applicable with little dependence on mineral compositions. It also indicates that the pressed powder method with Rigaku’s advanced correction technology is widely applicable throughout the iron ore industry, including suppliers, producers and steel manufacturers, with higher cost-efficiency and higher throughput than the conventional method.
Related products
ZSX Primus III NEXT
Affordable, high-end, tube-above Industrial WDXRF for the analysis of solid samples
Learn More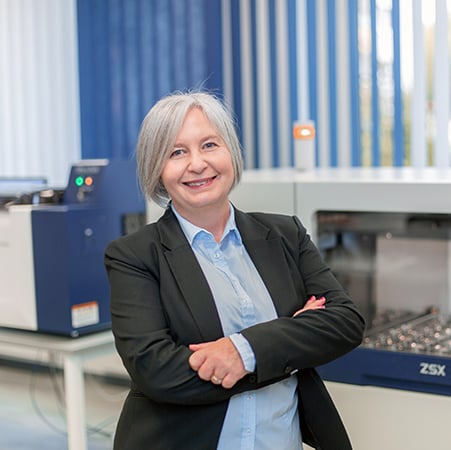
Contact Us
Whether you're interested in getting a quote, want a demo, need technical support, or simply have a question, we're here to help.