Cement Analysis by the Fusion Method According to ASTM C114-18
Introduction
Cement is one of the most important materials for construction. Many kinds of hydraulic cements with various physical properties, including Portland cement, are produced by changing the composition of clinker minerals; therefore, it is important to control the chemical composition of cement products and interim products.
Since the fusion method can eliminate sample heterogeneity problems, such as grain size and mineralogical effects, it is possible to obtain high accuracy for cement samples and also to establish calibrations using a variety of materials. Therefore, X-ray fluorescence (XRF) spectrometry by the fusion method has been the method of choice in cement production processes.
ASTM C114-18 covers chemical analysis of hydraulic cements. In this standard, mainly procedures of wet chemical analysis are described and XRF spectrometry is mentioned as an example of “Rapid Test Methods”. In practice, XRF spectrometry has been used for chemical composition analysis of cement owing to its simple sample preparation and high precision.
This application note demonstrates quantitative analysis for Portland cements by the fusion method according to ASTM C114-18 on Rigaku Simultix 15, a multi-channel simultaneous wavelength dispersive XRF (WDXRF) spectrometer.
Instrument
The Simultix 15 is a simultaneous WDXRF spectrometer with multiple channels, which enables simultaneous measurement of all the elements in analysis samples. The instrument is designed for rapid analysis with high reliability and stability for routine analysis of production control.
The Simultix 15 is equipped with either a 4 kW or a 3 kW X-ray tube and fixed channels optimized for the elements to be measured. Configurations with up to 30 fixed channels (optionally, 40 channels) are available for simultaneous analysis. High-performance scanning goniometer channels (optional) can also be substituted for some fixed channels. An intelligent Automatic Sample Changer (ASC), capable of placing up to 48 samples, is optionally available for high-demand jobs.
The operation software has been improved to facilitate daily use operation. The integrated “Flowbar” in the quantitative analysis software guides users through the calibration procedure.
ASTM C114-18 and calibration standard
The ASTM C114-18 standard has the following descriptions about “Rapid Test Method”:- Using the test method chosen, make single determinations for each analyte under consideration on at least seven CRM (Certified Reference Material) samples. Complete two rounds of tests on different days repeating all steps of sample preparations. Calculate the differences between values and averages of the values from the two rounds of tests.
- When seven CRMs are used in the qualification procedures, at least six of the seven differences between duplicates obtained of any single analyte shall not exceed the limits shown in Table 1 and the remaining differences by no more than twice that value.
- For each analyte and each CRM, the average obtained shall be compared to the certified concentrations. When seven CRMs are used in the qualification procedure, at least six of the seven averages for each analyte shall not differ from the certified concentrations by more than the value shown in Table 1, and the remaining average by more than twice that value.
The maximum permissible variations in analysis results defined in ASTM C114-18 are listed in Table 1. ASTM C114-18 directs that acceptable reference cements are NIST CRMs, or other reference cements traceable to the NIST CRMs. In this application note, seven NIST CRMs (SRM1881a, 1884a, 1885a, 1886a, 1887a, 1888a and 1889a) were used for calibration and a qualification test.
Table 1: Maximum permissible variation (unit: mass%)
Analysis component | Maximum difference between duplicates | Maximum difference of the average of duplicates from the certificate values |
SiO₂ | 0.16 | ±0.2 |
Al₂O₃ | 0.20 | ±0.2 |
Fe₂O₃ | 0.10 | ±0.10 |
CaO | 0.20 | ±0.3 |
MgO | 0.16 | ±0.2 |
SO₃ | 0.10 | ±0.1 |
Na₂O | 0.03 | ±0.05 |
K₂O | 0.03 | ±0.05 |
TiO₂ | 0.02 | ±0.03 |
P₂O₅ | 0.03 | ±0.03 |
ZnO | 0.03 | ±0.03 |
Mn₂O₃ | 0.03 | ±0.03 |
Sample preparation
For fusion, 0.8 g of the sample and 3.2 g of flux (lithium tetraborate 50% and lithium metaborate 50% in weight, pre-dried at 500°C) were weighed and mixed. The mixture was fused at 1050°C.
Measurement
Measurements were performed in vacuum on the Simultix 15 with a 4 kW Rh target X-ray tube. Table 2 shows measurement conditions of the analyzing crystals and detectors. Tube voltage and current applied was 40 kV-60 mA and all the elements were measured simultaneously with a counting time of 40 seconds.
Table 2: Measurement condition
Element | Si | Al | Fe | Ca |
Crystal | RX4 | PET | LiF(200) | LiF(200) |
Detector | F-PC | F-PC | S-PC | S-PC |
Element | Mg | S | Na | K |
Crystal | RX35 | NaCl | RX35 | LiF(200) |
Detector | F-PC | S-PC | F-PC | S-PC |
Element | Ti | P | Zn | Mn |
Crystal | LiF(200) | Ge | LiF(200) | LiF(200) |
Detector | S-PC | S-PC | S-PC | S-PC |
Calibration
The calibration results are summarized in Table 3. The calibration curves are shown in Figure 1. Matrix correction (theoretical alpha correction) was applied to the calibrations.
Table 3: Calibration results (unit: mass%)
Component | Calibration range | Accuracy |
SiO₂ | 18.637 - 22.38 | 0.043 |
Al₂O₃ | 3.875 - 7.06 | 0.035 |
Fe₂O₃ | 0.152 - 3.09 | 0.021 |
CaO | 57.58 - 67.87 | 0.083 |
MgO | 0.814 - 4.475 | 0.008 |
SO₃ | 2.086 - 4.622 | 0.021 |
Na₂O | 0.021 - 1.068 | 0.018 |
K₂O | 0.093 - 1.228 | 0.003 |
TiO₂ | 0.084 - 0.3663 | 0.002 |
P₂O₅ | 0.022 - 0.306 | 0.002 |
ZnO | 0.0048 - 0.107 | 0.001 |
Mn₂O₃ | 0.0073 - 0.2588 | 0.001 |
Figure 1: Calibration curves
The accuracy of calibration was calculated by the following formula:
$Accuracy = \sqrt{ \frac{\sum_i{(C_i-\hat{C}_i)^2}}{n-m} }$
$C_i$: calculated value of standard sample
$\hat{C}_i$: reference value of standard sample
n : number of standard samples.
m: degree of freedom (linear 2, quad. 3)
Qualification test for ASTM C114-18
Quantitative analyses have been carried out for the seven NIST SRMs of Portland cement using the calibration curves obtained above. The results are listed in the Table 4 comparing them with the ASTM C114-18 requirements.
Table 4: Qualification test results (unit: mass%)
Analysis component |
Analysis range | Difference between duplicates | Qualified | |
Limit (ASTM) | Maximum difference | |||
SiO₂ | 18.637-22.38 | 0.16 | 0.05 | ✓ |
Al₂O₃ | 3.875-7.06 | 0.20 | 0.01 | ✓ |
Fe₂O₃ | 0.152-3.09 | 0.10 | 0.003 | ✓ |
CaO | 57.58-67.87 | 0.20 | 0.14 | ✓ |
MgO | 0.814-4.475 | 0.16 | 0.01 | ✓ |
SO₃ | 2.086-4.622 | 0.10 | 0.01 | ✓ |
Na₂O | 0.021-1.068 | 0.03 | 0.006 | ✓ |
K₂O | 0.093-1.228 | 0.03 | 0.004 | ✓ |
TiO₂ | 0.084-0.3663 | 0.02 | 0.003 | ✓ |
P₂O₅ | 0.022-0.306 | 0.03 | 0.001 | ✓ |
ZnO | 0.0048-0.107 | 0.03 | 0.0004 | ✓ |
Mn₂ O₃ | 0.0073-0.2588 | 0.03 | 0.001 | ✓ |
Analysis component | Analysis range | Difference of the average of duplicate from the certificate values | Qualified | |
Limit (ASTM) | Maximum difference | |||
SiO₂ | 18.637-22.38 | ±0.2 | 0.08 | ✓ |
Al₂O₃ | 3.875-7.06 | ±0.2 | 0.05 | ✓ |
Fe₂O₃ | 0.152-3.09 | ±0.10 | -0.04 | ✓ |
CaO | 57.58-67.87 | ±0.3 | 0.19 | ✓ |
MgO | 0.814-4.475 | ±0.2 | 0.01 | ✓ |
SO₃ | 2.086-4.622 | ±0.1 | 0.03 | ✓ |
Na₂O | 0.021-1.068 | ±0.05 | 0.03 | ✓ |
K₂O | 0.093-1.228 | ±0.05 | 0.005 | ✓ |
TiO₂ | 0.084-0.3663 | ±0.03 | 0.003 | ✓ |
P₂O₅ | 0.022-0.306 | ±0.03 | 0.003 | ✓ |
ZnO | 0.0048-0.107 | ±0.03 | 0.001 | ✓ |
Mn₂O₃ | 0.0073-0.2588 | ±0.03 | 0.002 | ✓ |
The results prove that the analysis method demonstrated in this application note meets the requirements described in ASTM C114-18.
Repeatability test
Another test involving 10-times repeat measurements was carried out using the fused beads of NIST SRM 1884a and 1888a to demonstrate the stability of the instrument. The results of the 10-times measurements are tabulated in Table 5.
Table 5: Repeatability test results by 10-time measurement (unit: mass%)
Sample: NIST SRM 1884a | ||||
Analysis component | Certified value | Average | Standard deviation | R.S.D. % |
SiO₂ | 20.57 | 20.60 | 0.011 | 0.05 |
Al₂O₃ | 4.264 | 4.294 | 0.0068 | 0.16 |
Fe₂O₃ | 2.695 | 2.655 | 0.0022 | 0.08 |
CaO | 62.26 | 62.16 | 0.021 | 0.03 |
MgO | 4.475 | 4.475 | 0.0076 | 0.17 |
SO₃ | 2.921 | 2.899 | 0.0042 | 0.15 |
Na₂O | 0.2161 | 0.203 | 0.0037 | 1.82 |
K₂O | 0.997 | 0.998 | 0.0012 | 0.12 |
TiO₂ | 0.186 | 0.187 | 0.0013 | 0.72 |
P₂O₅ | 0.1278 | 0.131 | 0.0008 | 0.60 |
ZnO | 0.0101 | 0.010 | 0.0001 | 1.13 |
Mn₂O₃ | 0.0853 | 0.087 | 0.0004 | 0.49 |
Sample: NIST SRM 1888a | ||||
Analysis component | Certified value | Average | Standard deviation | R.S.D. % |
SiO₂ | 21.22 | 21.21 | 0.011 | 0.05 |
Al₂O₃ | 4.265 | 4.314 | 0.0062 | 0.14 |
Fe₂O₃ | 3.076 | 3.110 | 0.0025 | 0.08 |
CaO | 63.23 | 63.20 | 0.021 | 0.03 |
MgO | 2.982 | 2.972 | 0.0067 | 0.23 |
SO₃ | 2.131 | 2.129 | 0.0036 | 0.17 |
Na₂O | 0.1066 | 0.136 | 0.0035 | 2.55 |
K₂O | 0.526 | 0.523 | 0.0011 | 0.21 |
TiO₂ | 0.263 | 0.262 | 0.0014 | 0.52 |
P₂O₅ | 0.08 | 0.079 | 0.0008 | 1.00 |
ZnO | 0.107 | 0.107 | 0.0003 | 0.30 |
Mn₂O₃ | 0.1256 | 0.125 | 0.0005 | 0.41 |
Conclusion
The qualification test for ASTM C114-18 demonstrated that the test results on the Simultix 15 by the fusion method meet and/or exceed the requirements for analysis of hydraulic cement defined in ASTM C114-18.
The Simultix 15 is a simultaneous wavelength dispersive XRF spectrometer with multiple-channels, which enables simultaneous measurement of all the elements in analysis samples. In this application note, the counting time of the measurement was 40 seconds for twelve elements in cement.
Reference
ASTM C114-18 Standard Test Methods for Chemical Analysis of Hydraulic Cement
Related products
Simultix15
High-throughput tube-above multi-channel simultaneous WDXRF spectrometer analyzes Be through U.
Learn More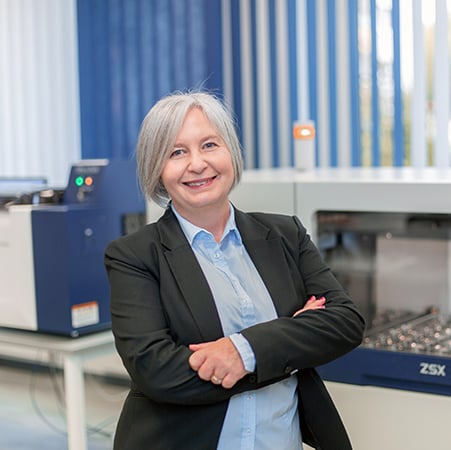
Contact Us
Whether you're interested in getting a quote, want a demo, need technical support, or simply have a question, we're here to help.