Multiple Element Determination of Nickel Sulfide Ores by the Pressed Powder Method on Simultix15
Introduction
Nickel is an essential base metal in modern industries. About 60% of nickel is used to make stainless steel. In recent years, the market price of nickel metal and the volume of production of primary nickel and ore have been increasing. Therefore, the demand in laboratories for accurate and fast analysis to determine multiple metal elements in ores is growing.
At mining sites, laboratories are often required to perform high volumes of analyses, up to a few hundred samples per day. However, wet chemical analysis, the conventional analytical technique for multiple metal determinations, is difficult to perform this scale because the method is time-consuming and requires significant analytical skill. Moreover, the large volume of liquid acid waste after conventional wet chemical analysis is an undesirable burden in many laboratories. X-ray fluorescence (XRF) analysis is a well-known technique to accurately and quickly determine multiple elements in samples. The pressed powder method in XRF spectrometry is the best solution in terms of simplicity of analysis and reduction of environmental impact. Since sulfide ore has a complex matrix owing to its various mineral assemblages, appropriate corrections for the matrix effect are required in XRF analysis. The conventional correction technique for metals in ores uses the Compton scattering as an internal standard (the Compton scattering ratio method) but the results were often not satisfactory to meet the requirements of the mining industry. Rigaku has developed an improved Compton scattering method that integrates a theoretical alpha correction so the analytical results are significantly improved.
This note demonstrates the improved method to determine multiple elements in nickel sulfide ores by the pressed powder method, which can cover from Run-Of-Mine to concentrate.
Instrument
The Simultix 15 is a simultaneous wavelength dispersive X-ray fluorescence (WDXRF) spectrometer with multiple-channels, which enables high-throughput analysis. The instrument is designed to provide reliable production control and stability for routine analysis applications.
The Simultix 15 is equipped with a 4 kW X-ray tube and fixed channels optimized for the elements to be measured. Up to 40 fixed channels are available (optional) for simultaneous analysis. High-performance scanning goniometer channels (optional) can also be substituted for some fixed channels. An intelligent Automatic Sample Changer (ASC), capable of placing up to 48 samples, is optionally available for high-demand jobs.
The tube-above optics of the Simultix 15 minimizes the contamination from sample spillage during powder sample measurements. This configuration means that pressed pellet samples can be prepared without adding any binding agents or with smaller amounts than usual, which simplifies sample preparation and is cost-effective by reducing binding agent usage. The powder trap attachment avoids trouble in the vacuum system caused by grains scattered from powder samples.
The operation software is improved facilitate daily-use operation. The newly integrated “Flowbar” in quantitative analysis guides users through calibration. The ”Quant Scatter FP” program is a unique optional function integrated with Rigaku FP program. It can be used to obtain theoretical alphas for the Compton scattering method applied to heavy elements in ore analysis. The ”Quant Scatter FP” function is available on the Simultix 15 system.
Standards and sample preparation
The standard samples used for calibration were 14 commercially available certified reference materials (CRMs). These standards are composed of nickel sulfide ore and concentrate. The range of nickel content in these CRMs is wide from 0.406 mass% to 11.7 mass%. Copper, cobalt and iron range from 0.022 mass% to 1.54 mass%, 0.013 mass% to 0.266 mass% and 6.84 mass% to 45.1 mass%, respectively.
The well-dried (2 hours at 105˚C) samples were ground with a chromium steel container and then pressed under pressure at 150 kN using sample cups without binding agent. In general, binding agents affect analysis results in the Compton scattering ratio method, therefore, it is strongly advisable to press samples without binding agents when the Compton scattering ratio method is applied.
Measurement and calibration
The Simultix 15 with a 4 kW Rh target X-ray tube was used to measure the Na, Mg, Al, Si, P, S, K, Ca, Ti, Mn, Fe, Co, Ni, Cu, Zn and As element lines, and the Rh-Kα Compton scattering line. For the Fe-Kα measurement, an attenuator was used to obtain appropriate intensity without changing tube loading. Counting time for all element lines was 40 seconds. The calibration equations for nickel, copper and iron are as follows:
$W_i = (AI_R^2+BI_R+C)\cdot(1+\sum{a_jW_j})$
$I_R = I_{i}/I_{scat}$
$a_j$: theoretical alpha of element j
$W_j$: weight fraction of element j
$I_{i}$: intensity of element i
$I_{Compton}$: intensity of Rh-Kα Compton line
$A, B, C$: constants
Table 1: Accuracy comparison between correction methods (unit : mass%)
Element | Concentration range | Typical accuracy of concentration | |
Rigaku correction | Conventional internal standard | ||
Ni | 0.401 – 11.7 | 0.070 | 0.12 |
Cu | 0.022 – 1.54 | 0.020 | 0.084 |
Fe | 6.84 – 26.9 | 0.79 | 2.6 |
Matrix correction coefficients (alphas) applied to the matrix correction in the calibrations were theoretically calculated by the built-in program using FP. The theoretical alphas for nickel, copper and iron calibrations were calculated taking into account the Compton scattering ratio by the “Quant Scattering FP” function.
Results
Calibration curves for nine selected components, Ni, Cu, Co, Fe, Ca, S, S, Al and Mg, are shown in Figure 1. As can be seen, the accuracy of the nickel calibration is excellent even over a wide concentration range. The conventional internal standard method using the Compton scattering ratio gives 0.12 mass% for the accuracy of calibration for the same concentration range. Table 1 shows a comparison of results applying the Rigaku correction method and the conventional internal standard method. It is obvious that the accuracy of the calibration to which the Rigaku correction method is applied is significantly improved. Calibration accuracies for all components measured in this study are listed in Table 2.
Figure 1: Calibration curves of representative components in nickel sulfide ores. Calibration curves of nickel, copper and iron use the Compton scattering ratio with theoretical alpha correction.
Table 2: Accuracy of the calibration curves (unit: mass% )
Element | Concentration range | Typical accuracy of calibration |
Ni | 0.406 – 11.7 | 0.070 |
Cu | 0.022 – 1.54 | 0.020 |
Co | 0.013 – 0.266 | 0.008 |
Zn | 0.007 – 2.67 | 0.004 |
As | 0.001 – 0.205 | 0.003 |
Fe | 6.84 – 45.1 | 0.79 |
Mn | 0.027 – 0.126 | 0.003 |
Ti | 0.039 – 1.07 | 0.011 |
Ca | 0.505 – 5.94 | 0.18 |
K | 0.019 – 1.14 | 0.021 |
S | 1.44 –26.9 | 0.78 |
P | 0.008 – 0.077 | 0.002 |
Si | 4.54 – 24.3 | 0.87 |
Al | 0.550 – 6.83 | 0.20 |
Mg | 1.18 – 19.6 | 0.91 |
Na | 0.053 – 1.86 | 0.097 |
Accuracy is calculated by the following formula:
$Accuracy = \sqrt{ \frac{\sum_i{(C_i-\hat{C}_i)^2}}{n-m} }$
$C_i$: calculated value of standard sample
$\hat{C}_i$: reference value of standard sample
n : number of standard samples.
m: degree of freedom (linear 2, quad. 3)
To demonstrate instrumental precision, 20 measurements were also performed with a nickel sulfide ore sample. The average and standard deviation for each component are shown in Table 3.
Table 3: Result of precision test (unit: mass%)
Element | Certified value | Average of 20 measurements | Std. dev. | RSD% |
Ni | 0.686 | 0.716 | 0.0007 | 0.10 |
Cu | 0.0222 | 0.0184 | 0.0001 | 0.43 |
Co | 0.0131 | 0.0153 | 0.00006 | 0.37 |
Zn | 0.0099 | 0.0060 | 0.00008 | 1.2 |
As | 0.0146 | 0.0138 | 0.00004 | 0.29 |
Fe | 6.84 | 6.90 | 0.006 | 0.083 |
Mn | 0.101 | 0.0971 | 0.0001 | 0.15 |
Ti | 0.216 | 0.196 | 0.0003 | 0.13 |
Ca | 2.79 | 2.61 | 0.003 | 0.13 |
K | 1.14 | 1.10 | 0.001 | 0.10 |
S | 1.44 | 1.74 | 0.001 | 0.067 |
P | 0.026 | 0.025 | 0.0008 | 0.66 |
Si | 24.02 | 23.24 | 0.009 | 0.041 |
Al | 4.79 | 4.32 | 0.002 | 0.054 |
Mg | 9.59 | 9.28 | 0.006 | 0.073 |
Na | 1.01 | 0.872 | 0.002 | 0.20 |
Conclusions
X-ray fluorescence spectrometry is rapid, precise and accurate method to meet the requirements of the mining industry.
A simultaneous multi-channel system is the best suited for laboratory at the mine site or at a beneficiation plant, where a high volume of sample analyses is required for quality and process control.
This application note demonstrates that an improved correction method using the “Quant Scatter FP” function, which is the combination of the Compton scattering ratio method and a theoretical alpha correction, is practically applicable for analysis of nickel sulfide ore and concentrates.
The pressed powder method with Rigaku’s advanced correction technology is widely available for mining industries, with higher cost-efficiency and higher throughput than conventional method
The Rigaku Simultix 15 has all the features stated above and is the best system for production and quality control of nickel ore mining.
Related products
Simultix15
High-throughput tube-above multi-channel simultaneous WDXRF spectrometer analyzes Be through U.
Learn More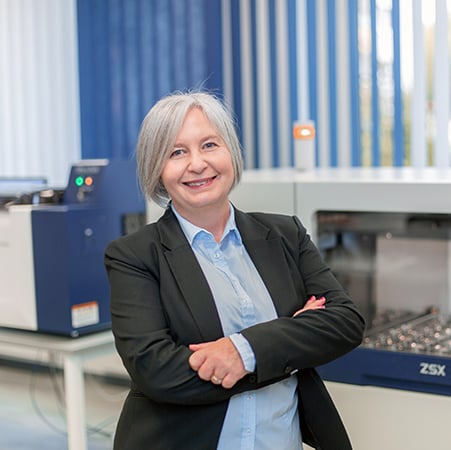
Contact Us
Whether you're interested in getting a quote, want a demo, need technical support, or simply have a question, we're here to help.