Lubricating Oil Analysis by Benchtop WDXRF according to ASTM D6443-14
Introduction
Lubricating oils are given specific functional properties by mixing additives with base oil. In order to assure consistent and desirable performance, it is very important to control the concentrations of the additives during the lubricant manufacturing process.
X-ray fluorescence (XRF) spectrometry has become increasingly popular for quantitative elemental analysis of base oils as well as additives and lubricant products due to its high precision and simple sample preparation. With liquids, sample preparation for XRF typically means simply pouring the sample into a plastic cell with a transparent film. Unlike other techniques, such as Inductively-Coupled Plasma Optical Emission Spectroscopy (ICP-OES), XRF does not require time-consuming processes such as chemical decomposition, digestion or serial dilution.
ASTM D6443-14 specifies the use of the wavelength dispersive (WD) XRF technique since it offers sufficiently high precision, resolution and light-element sensitivity to meet the industry’s needs.
Traditionally, WDXRF spectrometers have been large floor-standing models with substantial installation requirements and high replacement cost of faulty components. In its search for greater cost-efficiency, the lubricant industry is turning to tools that not only do the job, but are also easier and less costly to acquire, install and maintain.
This application note demonstrates the capability of low-cost, compact benchtop WDXRF spectrometer for quantitative elemental analysis of Ca, Cl, Cu, Mg, P, S and Zn in base oils, lubricating oils and additives according to ASTM D6443-14.
Instrument
The Supermini200 is a benchtop sequential WDXRF spectrometer designed specifically to deliver excellent performance while eliminating typical installation requirements such as cooling water, special power supply and large floor space.
Featuring a unique air-cooled 200 W X-ray tube, two detectors, programmable vacuum or helium atmosphere, and three analyzing crystals, the Supermini200 can analyze all relevant elements in just a few minutes with full spectral separation of all peaks and excellent sensitivity for light elements such as Mg, P and Cl.
The Windows®-based software used to operate the Supermini200 shares the same platform running Rigaku’s popular higher-power WDXRF ZSX family instruments. This means that it has the same advanced algorithms, multiple language support and an intuitive user-friendly interface that have made Rigaku the world’s leader in XRF instrumentation and industrial applications.
Standards and sample preparation
Organometallic reference standard samples for lubricating oil provided by AccuStandard®, Inc. were used as calibration standards.
Six grams of each sample was poured into a liquid cell (Chemplex® 1540) with 4.0 μm Prolene® (Chemplex® 416) as sample film. The cells are disposable and inexpensive.
Measurement Conditions
All elements were measured in helium atmosphere, using standard crystals, with the X-ray tube operating at 50 kV and 4.0 mA. Peak and background intensities were counted for each element line, and the total counting time was less than nine minutes.
Calibration
In accordance with ASTM D6443-14, empirical matrix corrections were applied to all analytes except Mg. The calibration results are listed in Table 1, with the corresponding calibration curves shown in Figure 1.
Table 1: Calibration results for all elements
Element | Calibration range (mass%) | Accuracy (mass%) | LLD (ppm) |
Ca | 0 – 0.50 | 0.0021 | 1.9 |
Cl | 0 – 0.15 | 0.0005 | 0.8 |
Cu | 0 – 0.05 | 0.0006 | 1.1 |
Mg | 0 – 0.20 | 0.0044 | 20 |
P | 0 – 0.15 | 0.0004 | 1.0 |
S | 0 – 0.75 | 0.0032 | 0.9 |
Zn | 0 – 0.15 | 0.0020 | 1.0 |
Figure 1: Calibration curve with matrix correction for lubricating oil
The calibration accuracies were calculated by the following formula:
$Accuracy = \sqrt{ \frac{\sum_i{(C_i-\hat{C}_i)^2}}{n-2} }$
$C_i$: calculated value of standard sample
$\hat{C}_i$: reference value of standard sample
n : number of standard samples.
The lower limits of detection (LLD) were calculated as follows:
$LLD = 3 \cdot \frac{1}{m} \cdot \sigma_B = \frac{3}{m} \cdot \sqrt{\frac{I_B}{1000 \cdot t}}$
$m$ : sensitivity of calibration (kcps/mass%)
$\sigma_B$ : standard deviation of blank intensity (kcps)
$I_B$ : blank intensity (kcps)
$t$ : counting time (s)
Analysis results
To confirm that the spectrometer’s repeatability performance is compliant with the requirement of the method, two aliquots of a representative sample were prepared and quantified. This process was repeated twenty times.
Table 2: Repeatability test results
Ca | Cl | Cu | Mg | |||||
Avg. | Diff. | Avg. | Diff. | Avg. | Diff. | Avg. | Diff. | |
1 | 0.0102 | 0.0001 | 0.0107 | 0.0000 | 0.0118 | 0.0002 | 0.0332 | 0.0020 |
2 | 0.0102 | 0.0001 | 0.0106 | 0.0002 | 0.0118 | 0.0001 | 0.0324 | 0.0004 |
3 | 0.0102 | 0.0000 | 0.0106 | 0.0001 | 0.0119 | 0.0001 | 0.0326 | 0.0000 |
4 | 0.0103 | 0.0001 | 0.0106 | 0.0000 | 0.0118 | 0.0002 | 0.0340 | 0.0027 |
5 | 0.0103 | 0.0001 | 0.0105 | 0.0002 | 0.0117 | 0.0000 | 0.0351 | 0.0005 |
6 | 0.0102 | 0.0000 | 0.0105 | 0.0002 | 0.0118 | 0.0002 | 0.0332 | 0.0033 |
7 | 0.0103 | 0.0002 | 0.0107 | 0.0001 | 0.0120 | 0.0001 | 0.0337 | 0.0044 |
8 | 0.0104 | 0.0001 | 0.0107 | 0.0000 | 0.0118 | 0.0004 | 0.0340 | 0.0039 |
9 | 0.0103 | 0.0001 | 0.0107 | 0.0000 | 0.0117 | 0.0001 | 0.0342 | 0.0043 |
10 | 0.0102 | 0.0001 | 0.0107 | 0.0001 | 0.0118 | 0.0001 | 0.0338 | 0.0050 |
11 | 0.0103 | 0.0003 | 0.0106 | 0.0001 | 0.0119 | 0.0002 | 0.0331 | 0.0035 |
12 | 0.0105 | 0.0001 | 0.0106 | 0.0001 | 0.0120 | 0.0000 | 0.0353 | 0.0009 |
13 | 0.0104 | 0.0002 | 0.0106 | 0.0001 | 0.0119 | 0.0002 | 0.0341 | 0.0032 |
14 | 0.0102 | 0.0003 | 0.0106 | 0.0001 | 0.0118 | 0.0001 | 0.0338 | 0.0025 |
15 | 0.0102 | 0.0003 | 0.0106 | 0.0001 | 0.0117 | 0.0000 | 0.0342 | 0.0016 |
16 | 0.0103 | 0.0000 | 0.0105 | 0.0000 | 0.0118 | 0.0001 | 0.0338 | 0.0008 |
17 | 0.0104 | 0.0002 | 0.0106 | 0.0001 | 0.0118 | 0.0000 | 0.0340 | 0.0005 |
18 | 0.0104 | 0.0002 | 0.0105 | 0.0003 | 0.0118 | 0.0001 | 0.0333 | 0.0009 |
19 | 0.0102 | 0.0002 | 0.0104 | 0.0001 | 0.0118 | 0.0002 | 0.0338 | 0.0019 |
20 | 0.0100 | 0.0003 0.0105 | 0.0001 0.0118 | 0.0002 0.0339 | 0.0016 | |||
Max | 0.0003 | 0.0003 | 0.0004 | 0.0050 | ||||
r | 0.0007 | 0.0007 | 0.0004 | 0.0053 | ||||
P | S | Zn | ||||||
Avg. | Diff. | Avg. | Diff. | Avg. | Diff. | |||
1 | 0.0100 | 0.0001 | 0.0474 | 0.0003 | 0.0113 | 0.0000 | ||
2 | 0.0100 | 0.0001 | 0.0476 | 0.0001 | 0.0114 | 0.0001 | ||
3 | 0.0100 | 0.0001 | 0.0477 | 0.0002 | 0.0115 | 0.0001 | ||
4 | 0.0100 | 0.0000 | 0.0476 | 0.0005 | 0.0114 | 0.0002 | ||
5 | 0.0101 | 0.0001 | 0.0474 | 0.0002 | 0.0113 | 0.0001 | ||
6 | 0.0100 | 0.0003 | 0.0477 | 0.0003 | 0.0114 | 0.0003 | ||
7 | 0.0098 | 0.0000 | 0.0478 | 0.0000 | 0.0115 | 0.0001 | ||
8 | 0.0100 | 0.0003 | 0.0476 | 0.0005 | 0.0114 | 0.0001 | ||
9 | 0.0102 | 0.0002 | 0.0477 | 0.0007 | 0.0113 | 0.0000 | ||
10 | 0.0102 | 0.0003 | 0.0479 | 0.0002 | 0.0113 | 0.0000 | ||
11 | 0.0101 | 0.0001 | 0.0479 | 0.0001 | 0.0114 | 0.0002 | ||
12 | 0.0102 | 0.0001 | 0.0478 | 0.0002 | 0.0115 | 0.0000 | ||
13 | 0.0101 | 0.0002 | 0.0477 | 0.0001 | 0.0115 | 0.0000 | ||
14 | 0.0100 | 0.0000 | 0.0478 | 0.0003 | 0.0115 | 0.0000 | ||
15 | 0.0099 | 0.0002 | 0.0477 | 0.0004 | 0.0116 | 0.0001 | ||
16 | 0.0099 | 0.0002 | 0.0474 | 0.0003 | 0.0115 | 0.0002 | ||
17 | 0.0100 | 0.0001 | 0.0474 | 0.0003 | 0.0114 | 0.0001 | ||
18 | 0.0101 | 0.0003 | 0.0474 | 0.0002 | 0.0114 | 0.0001 | ||
19 | 0.0100 | 0.0004 | 0.0474 | 0.0002 | 0.0114 | 0.0000 | ||
20 | 0.0098 | 0.0000 0.0474 | 0.0002 0.0114 | 0.0000 | ||||
Max | 0.0004 | 0.0007 | 0.0003 | |||||
r | 0.0008 | 0.0015 | 0.0005 |
The test data compiled in Table 2 shows the average and the difference between the two-aliquot measurement results. ASTM D6443-14 specifies that “the difference between successive test results obtained by the same operator with the same apparatus under constant operation conditions on identical test material...in the long run” must not exceed the values in Table 3, which shows the formula for the maximum allowed repeatability “r” of each analyte. All units in Table 3 are in terms of mass%, including the standards’ concentration.
“Max” indicated in Table 2 is the maximum actual obtained difference between successive results, while “r” represents the maximum permissible difference as prescribed by the ASTM method (see Table 3). Since “Max” never exceeds “r”, the repeatability performance of the Supermini200 easily satisfies the requirements of ASTM D6443-14.
Table 3: Repeatability as defined in ASTM D6443-14 (unit: mass%)
Element | Concentration range | Repeatability [r] |
Ca | 0.001 – 0.200 | 0.006914 (X+0.0007)0.5 |
Cl | 0.001 – 0.030 | 0.0356 (X+0.0086) |
Cu | 0.001 – 0.030 | 0.002267 (X+0.0013)0.4 |
Mg | 0.003 – 0.200 | 0.01611 (X+0.0008)0.333 |
P | 0.001 – 0.200 | 0.02114 X0.7 |
S | 0.030 – 0.800 | 0.02371 X0.9 |
Zn | 0.001 – 0.200 | 0.01225 X0.7 |
Note) X: concentration in mass%
Qualitative scans of each analyte element are shown in Figure 2 which demonstrate the excellent peak -to-background ratio and spectral resolution of the wavelength-dispersive technology in the Rigaku Supermini200.
Figure 2: Qualitative chart
Conclusions
This application note demonstrates that lubricating oils and additives can be routinely analyzed with excellent accuracy, sensitivity and repeatability using a benchtop WDXRF spectrometer with minimal installation requirements.
In particular, the Rigaku Supermini200 sequential WDXRF spectrometer meets the specifications of ASTM D6443-14, as well as those of ASTM D4927-10, which applies to higher concentrations of additive elements.
Reference
ASTM D6443-14 (2019) Standard Test Method for Determination of Calcium, Chlorine, Copper, Magnesium, Phosphorus, Sulfur, and Zinc in Unused Lubricating Oils and Additives by Wavelength Dispersive X-ray Fluorescence Spectrometry (Mathematical Correction Procedure)
Related products
Supermini200
Benchtop tube below sequential WDXRF spectrometer analyzes O through U in solids, liquids and powders
Learn More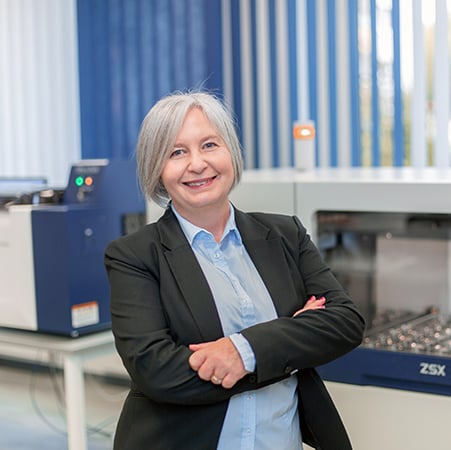
Contact Us
Whether you're interested in getting a quote, want a demo, need technical support, or simply have a question, we're here to help.