Fast and Accurate Determination of the Composition of Natural and Processed Iron Ores by the Fusion Method on Simultix 15
Introduction
Iron is the most common metal in industrial use. Modern infrastructure cannot be realized without iron alloys. The most dominant raw material for making metallic iron is iron ore. Currently, a huge volume of iron ore is traded in the world market. Although other factors affect iron ore prices such as ore size, ore type, physical properties, chemical composition and content of impurities, etc., ore grade (total iron content), in iron ore is the most critical factor for pricing. Therefore, highly accurate analysis to determine the total iron content is required.
In mining sites and agglomeration plants, it is often necessary to analyze hundreds of samples per day. However, it is difficult to perform so many analyses by wet chemical analysis, a traditional technique for total iron determination. In addition to accuracy, analysis methods must also be cost effective, which mean quick and simple.
X-ray fluorescence (XRF) spectrometry is familiar as a fast, simple and accurate method to determine chemical composition in solid and liquid materials, so it is widely used for quality and process control in the industrial sector.
The fused bead sample preparation technique can provide the best results from XRF analysis. The technique is optimal for powder samples since it can eliminate common sources of error, such as mineralogical and grain size effects.
For some error factors specific to the fusion method, Rigaku continues to develop bead correction functions to improve analytical results.
This note demonstrates an advanced method to determine the composition of total iron and other components in iron ore by the fusion method, which widely covers crude iron ores (low and high content iron ores) and agglomerates (pellet and sinter).
Instrument
The Simultix 15 is a simultaneous wavelength dispersive X-ray fluorescence (WDXRF) spectrometer with multiple-channels, which enables high-throughput analysis. The instrument is designed to provide reliable production control and stability for routine analysis applications.
The Simultix 15 is equipped with a 4 kW X-ray tube and fixed channels optimized for the elements to be measured. Up to 40 fixed channels are available (optional) for simultaneous analysis. High-performance scanning goniometer channels (optional) can also be substituted for some fixed channels. An intelligent Automatic Sample Changer (ASC), capable of placing up to 48 samples, is optionally available for high-demand jobs.
The tube-above optics of the Simultix 15 minimizes the contamination from sample drop during powder sample measurements. With this configuration, pressed pellet samples can be prepared without adding any binding agents or with smaller amounts than usual, which simplifies sample preparation and is cost-effective by reducing binding agent usage. The powder trap attachment avoids trouble in the vacuum system caused by particles scattered from powder samples.
The tube-above optics of the Simultix 15 is the best solution for daily operation for both pressed pellet and fused bead sample analysis.
The operation software is improved and facilitates daily-use operation. The newly integrated “Flowbar” in quantitative analysis guides users through calibration.
Standards and sample preparation
The standard samples used for calibration were 25 commercially available certified reference materials (CRMs). These standards are composed of hematite ore, magnetite ore, iron sand, limonite, iron ore sinter, pellet and pure iron oxide. The range of total iron concentration in these CRMs is wide from 24.7 mass% to 71.1 mass%, and the silica content ranges from 0.5 mass% to 20.0 mass%.
The well-dried (2 hours at 105°C) samples were fused with a flux of lithium tetraborate (Li₂B₄O₇) with a sample-to-flux ratio of 1:10 using a fusion machine.
Additive reagents as a releasing agent and an oxidizing agent were 10% lithium iodide solution and NaNO₃, respectively.
Although some iron ores are highly hydroscopic, sample calcination before making fused beads is not required since loss on ignition (LOI) during fusion can be corrected when making calibration curves by using theoretical alphas considering LOI. As the dilution ratio (sample-to-flux ratio) can also be corrected together with matrix effects, it is not necessary to weigh sample and flux exactly when making fusion beads. Reading values from a balance during weighing can be used to correct the dilution ratio.
Measurement and calibration
The Simultix 15 with a 4 kW Rh target X-ray tube was used to measure the element lines of Fe, Si, Al, P, Mg, S, Ca, K, Ti, Mn and V. For the Fe-Kα measurement, the attenuator function was used to obtain appropriate intensity without changing tube loading. The counting time was 40 s.
Calibrations for all components used the following equation:
$W_i = (BI_I+C)\cdot(1+\sum{a_jW_j})$
$a_j$: theoretical alpha of element j
$W_j$: weight fraction of element j
$I_{i}$: intensity of element i
$B, C$: constants
Figure 1: Calibration curves of representative components in iron ores. open circle: uncorrected, blue diamond: corrected
Matrix correction coefficients (alpha) applied to correct the matrix effect in the calibrations were theoretically calculated by a built-in program using Fundamental Parameters (FP). The theoretical alphas for iron ore calibration were calculated taking LOI info consideration by the FP program.
Results
Calibration curves for typical components, including total Fe₂O₃, SiO₂, Al₂O₃, MnO and P₂O₅ are shown in Figure 1. As shown in this figure, the accuracy of the total iron calibration is excellent.
Calibration accuracy for all components measured in this demonstration are listed in Table 1.
Table 1: Accuracy of the calibration curves (unit : mass% )
Component (Element) | Concentration range | Typical accuracy of calibration |
Fe₂O₃ (Total Fe) |
35.3 - 101.6 (24.7 - 71.1) |
0.10 (0.071) |
SiO₂ | 0.47 - 20.0 | 0.11 |
CaO | 0.016 - 22.0 | 0.066 |
MnO | 0.023 - 1.31 | 0.0079 |
Al₂O₃ | 0.27 - 7.24 | 0.033 |
TiO₂ | 0.023 - 7.77 | 0.011 |
MgO | 0.013 - 3.45 | 0.035 |
P₂O₅ (P) |
0.018 - 1.63 (0.008 - 0.711) |
0.0096 (0.0042) |
SO₃ (S) |
0.002 - 2.11 (0.0008 - 0.845) |
0.026 (0.010) |
K₂O | 0.0028 - 0.717 | 0.0026 |
V₂O₅ | 0.0035 - 0.82 | 0.0067 |
The accuracy is calculated by the following formula:
$Accuracy = \sqrt{ \frac{\sum_i{(C_i-\hat{C}_i)^2}}{n-m} }$
$C_i$: calculated value of standard sample
$\hat{C}_i$: reference value of standard sample
n : number of standard samples.
m: degree of freedom (linear 2, quad. 3)
Figure 2: Correlation of total Fe value between XRF and chemical analysis.
Using the established calibration curves, all standard samples were analyzed as unknown samples. Figure 2 shows the correlation of total Fe content between the XRF value and the chemical value. The calculated SEE (standard error of estimate) of total Fe is 0.10 mass% in this demonstration by the Simultix 15. The result is excellent in such a wide concentration range.
Conclusions
X-ray fluorescence spectrometry is a rapid, precise and accurate analysis method that meets the requirements of iron ore industries. It can also minimize cost and time in iron ore analysis. A multi-channel system is best-suited to mine sites or plant laboratories, where voluminous sample analysis is required for quality and process control.
The fused bead method is the best technique for the XRF method to determine iron content of various iron oxides with high precision for samples covering a wide concentration range.
Rigaku’s advanced bead correction function has higher cost-efficiency and throughput than conventional methods, making it possible for all iron ore industry sectors such as suppliers, producers and steel manufacturers.
Rigaku Simultix 15 has all the features stated above and is the best system for production and quality control of iron ore products.
Related products
Simultix15
High-throughput tube-above multi-channel simultaneous WDXRF spectrometer analyzes Be through U.
Learn More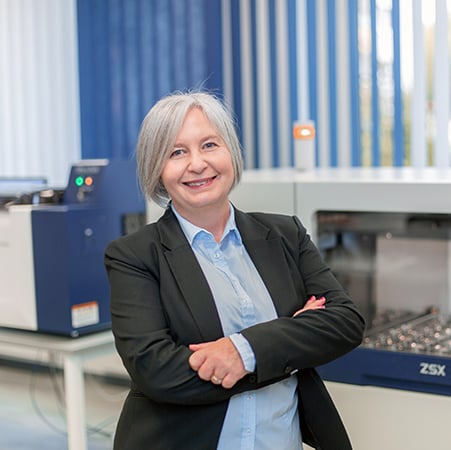
Contact Us
Whether you're interested in getting a quote, want a demo, need technical support, or simply have a question, we're here to help.