Accurate Determination for Elements in Laterite Ores by Pressed Powder Method
Introduction
Nickel laterite is one of the two types of ores for nickel extraction. The other type of ore is sulfide. Currently, 40% of the world’s nickel production is obtained from laterite ores. Its share is however likely to increase since most ore reserves and a majority of nickel mining projects currently under development are laterite deposits.
In nickel laterite mining, nickel and cobalt are target metals that represent ore grade. Iron and magnesium in laterite ore are indicative elements to determine extraction method, which is hydrometallurgical or pyrometallurgical process.
In modern resource industries, demand for accurate and quick determination of elements in ores is increasing in order to efficiently operate mining and processing. Wet chemical analysis, which is the traditional analytical technique for elemental determination, requires time and expertise for sample preparation and is therefore not suited for the rapid analysis of large number of samples.
X-ray fluorescence spectrometry (XRF) with pressed powder method can overcome these problems. For the analysis of laterites by XRF, to detect trace amount of cobalt, high spectral resolution is required since a large iron peak is present adjacent to the cobalt peak in the spectrum. In addition, high sensitivity is required for the analysis of light elements such as magnesium.
Wavelength dispersive XRF (WDXRF) can meet both of these requirements.
This note demonstrates an improved method to determine multiple elements in nickel oxide ores by pressed powder method.
Instrument
The Supermini200 is a unique benchtop sequential WDXRF spectrometer with high spectral resolution and high sensitivity for light elements. The spectrometer is designed to minimize installation utilities such as cooling water, power supply and installation space. For the analysis of light elements, the newly developed sealed proportional detector (S-PC) can be substituted (option) for the conventional flow proportional detector (F-PC). Since the S-PC eliminates the need for an external P10 (detector) gas cylinder, the Supermini200 can be a truly utility-free WDXRF instruments. It is equipped with an air-cooled 200W X-ray tube and up to three analyzing crystals allowing analysis of element oxygen to uranium.
The functionally versatile software allows easy setup of various types of applications. In particular, the flowbar guides the user step by step for the setting up of quantitative and qualitative analysis conditions.
The user friendly interface of the semi-quantitative analysis program “SQX” allows quick elemental determination of unknown samples without the need for reference materials.
Quant Scatter FP function
"Quant Scatter FP” is a unique function integrated Rigaku Fundamental Parameter (FP) system. The function is able to generate dedicated theoretical alphas to correct for matrix effects in empirical calibration curve by the internal standard method using scattering X-rays. The internal standard method using scattering X-rays (Compton scattering X-ray) without theoretical alphas has been preferred for heavy element analysis in some ores because of its ease of use. However, this conventional method does not fully correct for matrix effects especially for ore samples with high heavy element content. Rigaku’s correction scheme overcomes this problem by integrating the Compton scattering internal standard correction method with theoretical alpha correction by FP method. This advanced correction method for powder samples provides improved analysis results of ores.
”Quant Scatter FP” function (optional) is available for Supermini200 as well as Rigaku Simultix and ZSX Primus family.
Standard and sample preparation
The standard samples used for calibration are commercially available 14 certified reference materials (CRMs). These standards are composed of typical nickel laterites including saprolite and transitional type ores. This implies that these references cover ores from almost the entire stratigraphic profile in typical laterite deposits. Concentration range of nickel and cobalt in these CRMs is from 0.37 to 2.9 and 0.021 to 0.090 mass%. Iron and magnesium content ranges from 8.9 to 47 mass%, 1.2 to 17 mass%, respectively. Careful and consistent pulverization is quite essential to obtain good results because mineral assemblages are different depending on ore type. In addition, since laterite ores are highly hydroscopic, it is recommended to measure the specimen immediately after pelletization.
The well-dried (2 hours at 105°C) samples were ground and then pressed at 200 kN using sample cup. Generally, adding binder for pelletization introduces a potential source of analytical error in internal standard method using Compton scattering X-rays. Therefore, applications requiring high degree of accuracy should avoid use of binder.
Measurement and calibration
Supermini200 was used for the measurement of Ni, Co, Cu, Zn, Cr, Fe, Na, Mg, Si, Al, P, S, Ca, K, Ti and Mn element lines. Pd-Kα Compton scattering X-ray which is used for correction was also measured.
The calibration equation for nickel, iron and zinc is as follows:
$W_i = (AI_R^2 + BI_R + C) \cdot (1+\sum\alpha_jW_j)$
$I_R$ = $\frac{I_i}{I_{Compton}}$
$α_j$ : theoretical alpha of element j
$W_j$ : weight fraction of element j
$I_i$ : intensity of element i line
$I_{Compton}$ : intensity of Pd-Kα Compton line
$A, B, C$ : constant
Calibration for other components uses the following equation:
$W_i = (BI_i+C) \cdot (1+\sum\alpha_jW_j)$
$α_j$ : theoretical alpha of element j
$W_j$ : weight fraction of element j
$I_i$ : intensity of element i line
$B, C$ : constant
Matrix correction coefficients (alpha) applied to the calibrations are theoretically calculated by the FP software. The theoretical alphas for nickel, iron and zinc calibration are calculated by taking the Compton scattering internal standard into consideration by the Quant Scattering FP function integrated in the software.
Results
Calibration curves for Ni, Co, Fe, Mg, Al and Ca are shown in Figure 1. Aluminum, calcium and magnesium are elements of interest as well. It is preferred that the content of these elements are low, since they cause excessive consumption of sulfuric acid during the metal extraction process when the laterite ore is leached.
Calibration accuracies for all measured elements are listed in Table 1.
The accuracy of calibration is calculated by following the equation:
$Accuracy = \sqrt{ \frac{\sum_i{(C_i-\hat{C}_i)^2}}{n-m} }$
$C_i$: calculated value of standard sample
$\hat{C}_i$: reference value of standard sample
n : number of standard samples.
m: degree of freedom (linear 2, quad. 3)
The Rigaku correction method is compared to the conventional internal standard method and theoretical alpha correction. Results are shown in Table 2.
One saprolite and a transitional type ore were measured 10 times to demonstrate the instrument’s high precision. Results are summarized in Table 3 and 4. From rough estimation on the basis of these repeatability tests, 0.1 mass% of LOQ (limit of quantitation) is expected in magnesium analysis.
Figure 1: Calibration curves of representative elements in nickel laterite ores. Calibration curves of nickel, iron and zinc use Compton scattering internal standard combined with theoretical alpha correction. Blue: Corrected (certified), Yellow: Corrected (uncertified), Circle: Uncorrected.
Table 1: Accuracy of calibration curves (unit: mass%)
Element | Concentration range | Typical accuracy of calibration |
Ni | 0.37 - 2.9 | 0.030 |
Co | 0.002 - 0.090 | 0.0031 |
Fe | 8.9 - 47 | 0.27 |
Mg | 1.2 - 17 | 0.32 |
Na | 0.006 - 0.47 | 0.016 |
Al | 0.62 - 4.5 | 0.19 |
Si | 3.2 - 33 | 0.71 |
P | 0.002 - 0.017 | 0.0010 |
S | 0.002 - 1.3 | 0.016 |
K | 0.009 - 0.28 | 0.0018 |
Ca | 0.095 - 9.0 | 0.021 |
Ti | 0.012 - 0.21 | 0.0014 |
Cr | 0.14 - 1.8 | 0.022 |
Mn | 0.009 - 0.28 | 0.0067 |
Cu | 0.085 - 0.58 | 0.0019 |
Zn | 0.005 - 0.14 | 0.0017 |
Table 2: Comparison among correction methods for iron (unit : mass% )
Standard Sample | Chemical value (Fe) | Correction method | ||
Rigaku correction | Theoretical alpha | Conventional internal standard | ||
A | 47.46 | 47.49 | 47.73 | 47.45 |
B | 14.4 | 14.1 | 14.3 | 13.7 |
C | 9.68 | 9.66 | 9.52 | 9.33 |
D | 14 | 14.8 | 15.2 | 14.4 |
E | 15.2 | 14.8 | 14.9 | 13.7 |
F | 10.6 | 10.9 | 10.8 | 10.7 |
G | 20.72 | 20.66 | 20.23 | 20.48 |
H | 8.90 | 9.00 | 9.10 | 9.18 |
I | 27.57 | 27.72 | 27.60 | 27.45 |
J | 10.45 | 10.44 | 10.60 | 10.75 |
K | 24.76 | 24.75 | 24.16 | 25.20 |
L | 17.23 | 16.99 | 17.17 | 17.37 |
M | 11.48 | 11.41 | 11.69 | 11.98 |
N | 12.70 | 12.54 | 12.80 | 13.41 |
Standard error of estimate | 0.28 | 0.49 | 0.55 |
Table 3: Result of precision test for saprolite ore (unit : mass% )
Element | Certified value | Average of 10 measurements | Std. dev. | RSD% |
Ni | 2.10 | 2.15 | 0.007 | 0.32 |
Co | 0.0424 | 0.0399 | 0.0006 | 1.5 |
Fe | 11.48 | 11.45 | 0.02 | 0.19 |
Mg | 13.73 | 13.27 | 0.02 | 0.19 |
Na | 0.020 | 0.029 | 0.003 | 12 |
Al | 1.44 | 1.39 | 0.003 | 0.23 |
Si | 20.05 | 19.87 | 0.04 | 0.20 |
P | 0.0018* | 0.0018 | 0.0003 | 14 |
S | - | 0.010 | 0.001 | 12 |
K | 0.0093* | 0.0108 | 0.0008 | 7.5 |
Ca | 0.229 | 0.215 | 0.0008 | 0.38 |
Ti | 0.020 | 0.021 | 0.0006 | 3.0 |
Cr | 0.557 | 0.525 | 0.003 | 0.56 |
Mn | 0.203 | 0.202 | 0.001 | 0.57 |
Cu | 0.0041 | 0.0058 | 0.0002 | 2.9 |
Zn | 0.0184 | 0.0170 | 0.0002 | 1.0 |
* Uncertified
Table 4: Result of precision test for transitional ore (unit : mass% )
Element | Certified value | Average of 10 measurements | Std. dev. | RSD% |
Ni | 1.02 | 1.01 | 0.005 | 0.49 |
Co | 0.0899 | 0.0873 | 0.0007 | 0.85 |
Fe | 27.57 | 27.88 | 0.1 | 0.41 |
Mg | 1.81 | 1.91 | 0.009 | 0.49 |
Na | 0.0056 | 0.0050 | 0.003 | 63 |
Al | 2.42 | 2.19 | 0.003 | 0.14 |
Si | 19.71 | 19.53 | 0.04 | 0.20 |
P | 0.0074 | 0.0078 | 0.0004 | 4.9 |
S | - | 0.012 | 0.001 | 10 |
K | 0.0086* | 0.0083 | 0.0008 | 9.1 |
Ca | 0.165 | 0.184 | 0.0008 | 0.46 |
Ti | 0.035 | 0.036 | 0.0007 | 1.87 |
Cr | 1.20 | 1.22 | 0.006 | 0.5 |
Mn | 0.525 | 0.516 | 0.003 | 0.56 |
Cu | 0.0060 | 0.0040 | 0.0002 | 5.9 |
Zn | 0.0287 | 0.0277 | 0.0003 | 0.97 |
Conclusions
This application note demonstrates that it is possible to accurately analyze nickel oxide ores with wide concentration ranges from low to high grade nickel laterite by the pressed pellet method.
The results also indicate that Supermini200 is applicable to ore characterization and discrimination analysis for most stratigraphic profiles in typical laterite deposits.
The pressed powder method with Rigaku’s advanced correction technology can play a valuable role in various fields such as elemental analysis in exploration, metal extraction as well as quality and process control in mining and mineral processing.
Related products
Supermini200
Benchtop tube below sequential WDXRF spectrometer analyzes O through U in solids, liquids and powders
Learn More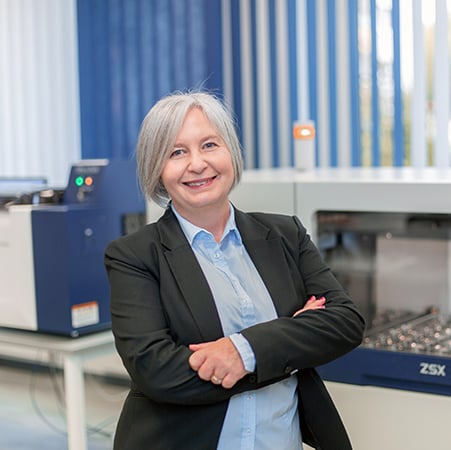
Contact Us
Whether you're interested in getting a quote, want a demo, need technical support, or simply have a question, we're here to help.