Fuel Cell Technologies
The widespread adoption of cleaner transportation depends on reliable quality control solutions. It is essential in scaling up operations and driving cost reductions in manufacturing processes. For fuel cell manufacturing, profiling the substrate or loading is crucial. In-line EDXRF provides real-time quality control throughout these processes.
NEX LS, an in-line measurement system, provides continuous results reporting for quick defect detection in catalyst layers. Its analytical head sweeps back and forth across a moving web, and data is displayed as a graphical cross-direction and machine-direction profile. It offers real-time quality control of platinum, iridium, or other loadings used in PEM fuel cell production.
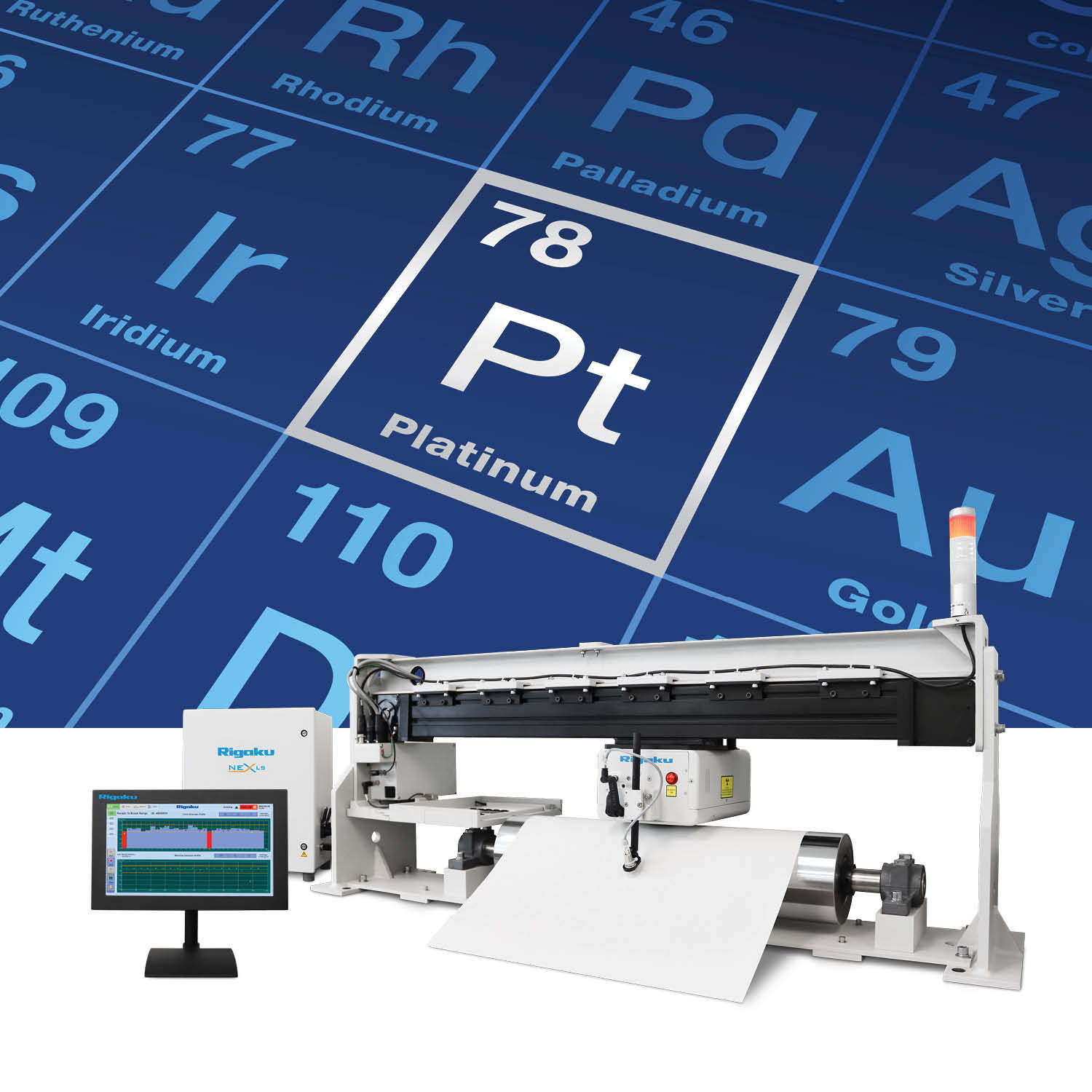
Why choose EDXRF?
In-line solutions for fuel cell loadings
Whether monitoring platinum and iridium or exploring other fuel cell loadings, NEX LS helps ensure quality and uniformity. This system offers continuous on-line inspection of these without the need to stop production for at-line checks. NEX LS helps you make real-time decisions and achieve reliable fuel cell loading quality control.
- Cross-direction and machine-direction profiling
- Supports user-defined measurement patterns
- Continuous monitoring for quick defect detection
- Roll reporting capabilities for quality records or audit trails
- Compact design and easy self-installation
- Configurable to meet your process control needs
- Easy automatic calibration and operation
- Minimal routine maintenance and 2-year warranty
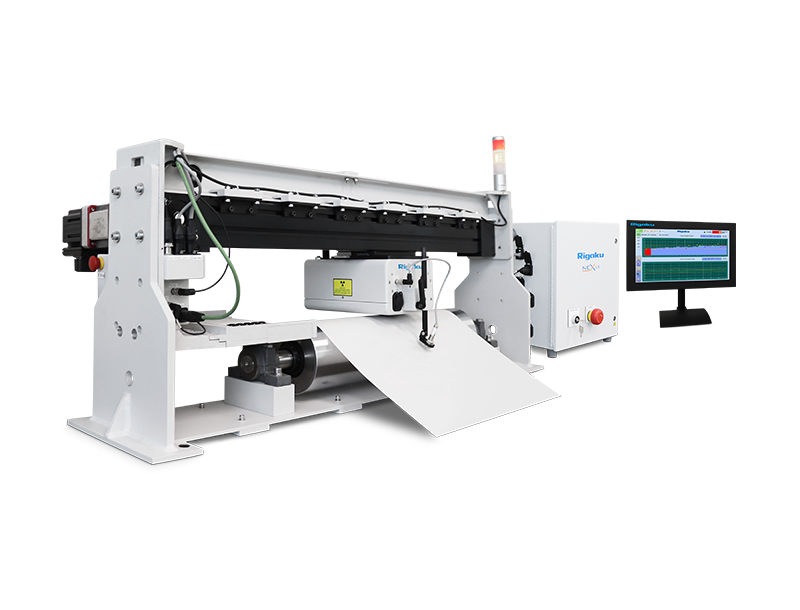
See NEX LS in action
How does NEX LS work?
NEX LS features EDXRF technology, a non-destructive technique that offers valuable information about the material or products as they are being produced. NEX LS serves web applications by performing real-time coat weight analysis.
The measuring head, mounted on a rigid beam, is equipped with a linear traversing mechanism ensuring constant head-to-surface distance. Where needed, the elemental composition of a coating is measured directly. In contrast, coat weight (or coating thickness) may be measured directly (where the counting rate for an element is proportional to thickness) or indirectly by measuring attenuation of some substrate element (where the counting rate is negatively correlated to thickness).
When the analytical head sweeps back and forth across a moving web, source X-rays enter the product, exciting atoms in the material. The elements in the coating excite and fluoresce characteristic X-rays back to the detector. Users can choose full scanning mode or fixed analysis positions. The scanner transmits these measurements to a console box and industrial touchscreen computer, and real-time data displays as a graphical cross-direction and machine-direction profile.
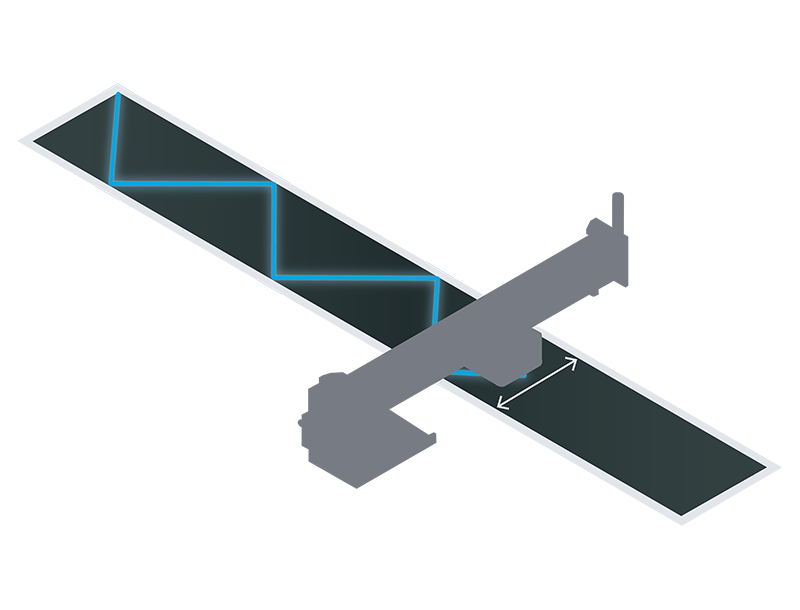
Full scanning analysis
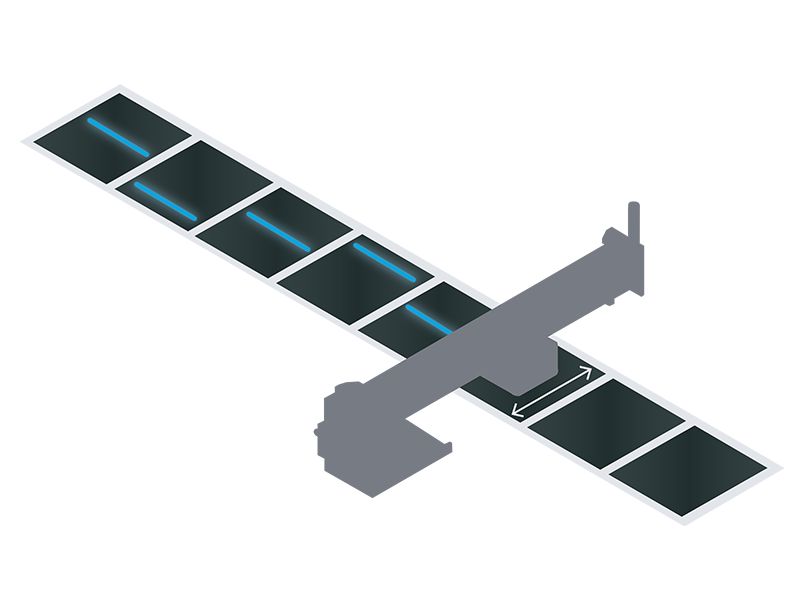
Fixed analysis solutions
Recommended products
In-line EDXRF for fuel cell technology
For in-line analysis NEX LS
Recommended for continuous measurement, monitoring, and control of platinum, iridium, or other loadings used in PEM fuel cell production.
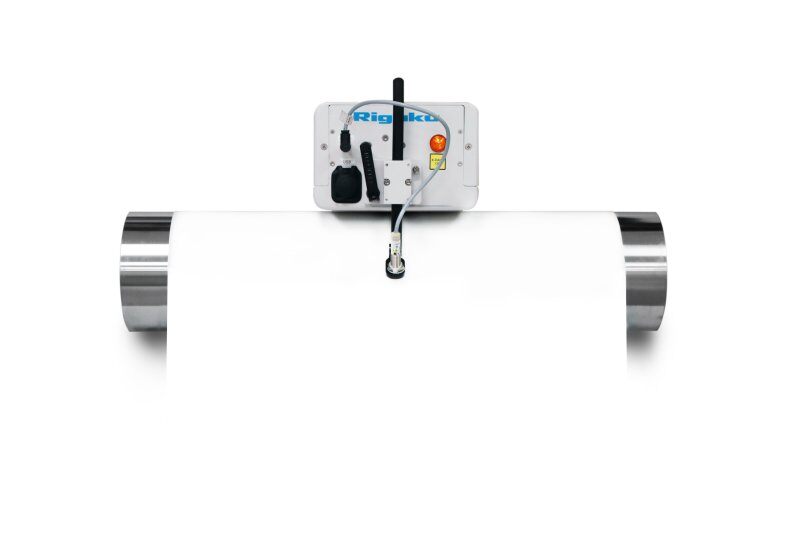
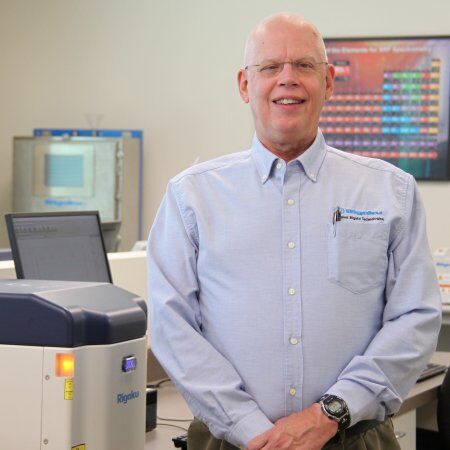
Contact Us
Whether you're interested in getting a quote, want a demo, need technical support, or simply have a question, we're here to help.