NEX DE Series—Analysis of Alloy Powders for Metal 3D Printing
Scope
The analysis of alloy powders used for 3D printing is demonstrated.
Background
DMLS (Direct Metal Laser Sintering) is an industrial metal 3D printing method that fuses layers of fine metal powder particles, creating a metal part layer by layer. Metal 3D printing techniques are ideal for manufacturing complex metal shapes that can be expensive or impossible to produce using traditional manufacturing methods. Metal 3D printed parts are typically stronger and denser than those made by traditional casting. The DMLS process is used for prototyping metal parts and low volume manufacturing, eliminating expensive and time-consuming tooling. When mixing various metal alloy powders, it is important to monitor the elemental compositions of the raw materials and powder mixtures to ensure proper alloy balances for the parts being produced. Applied Rigaku Technologies offers the Rigaku NEX DE EDXRF spectrometer for fast and simple analysis of metal alloy powders used in metal 3D printing.
Analytical
Sample ID: Al-Si-Mg | ||
Component | Result | Stat. error |
Mg | 0.126 | 0.0071 |
Al | 87.4 | 0.02 |
Si | 12.2 | 0.0105 |
P | ND | 0.0009 |
S | ND | 0.0005 |
Cl | ND | 0.0003 |
Ti | ND | 0.0018 |
V | 0.0111 | 0.0012 |
Cr | (0.0044) | 0.0007 |
Mn | 0.0038 | 0.0005 |
Fe | 0.294 | 0.0016 |
Co | ND | 0.0003 |
Ni | 0.0081 | 0.0002 |
Cu | 0.0045 | 0.0001 |
Zn | 0.0033 | <0.0001 |
Ga | 0.0080 | 0.0001 |
Y | 0.0002 | <0.0001 |
Nb | (0.0002) | <0.0001 |
Mo | 0.0010 | <0.0001 |
Sn | (0.0002) | <0.0001 |
Pb | 0.0009 | <0.0001 |
Sample ID: Ti-Al- V | ||
Component | Result | Stat. Error |
Mg | ND | 0.0303 |
Al | 4.49 | 0.0117 |
Si | ND | 0.0011 |
P | ND | 0.0006 |
S | ND | 0.0003 |
Cl | ND | 0.0003 |
Ti | 90.6 | 0.0334 |
V | 4.59 | 0.0153 |
Cr | ND | 0.0060 |
Mn | (0.0046) | 0.0013 |
Fe | 0.238 | 0.0028 |
Co | ND | 0.0006 |
Ni | 0.0294 | 0.0007 |
Cu | 0.0106 | 0.0004 |
Zn | (0.0012) | 0.0002 |
Ga | 0.0076 | 0.0002 |
Y | (0.0002) | <0.0001 |
Nb | 0.0026 | 0.0002 |
Mo | 0.0022 | 0.0002 |
Sample ID: PHSS | ||
Component | Result | Stat. error |
Mg | ND | 0.0097 |
Al | 0.0247 | 0.0031 |
Si | 0.528 | 0.0016 |
P | ND | 0.0004 |
S | ND | 0.0003 |
Cl | ND | 0.0002 |
Ti | ND | 0.0021 |
V | ND | 0.0013 |
Cr | 16.3 | 0.0208 |
Mn | (0.0252) | 0.0067 |
Fe | 75.6 | 0.0186 |
Co | 0.202 | 0.0061 |
Ni | 3.70 | 0.0107 |
Cu | 3.16 | 0.0086 |
Zn | (0.0022) | 0.0006 |
Ga | ND | 0.0004 |
Y | ND | <0.0001 |
Nb | 0.289 | 0.0019 |
Mo | 0.0158 | 0.0005 |
Sample ID: 316LSS | ||
Component | Result | Stat. error |
Mg | ND | 0.0105 |
Al | 0.125 | 0.0031 |
Si | 0.480 | 0.0016 |
P | ND | 0.0005 |
S | ND | 0.0008 |
Cl | ND | 0.0002 |
Ti | ND | 0.0024 |
V | ND | 0.0017 |
Cr | 18.5 | 0.0240 |
Mn | 0.938 | 0.0087 |
Fe | 65.5 | 0.0237 |
Co | 0.208 | 0.0065 |
Ni | 11.8 | 0.0183 |
Cu | 0.0905 | 0.0018 |
Zn | ND | 0.0005 |
Ga | ND | 0.0004 |
Y | ND | 0.0001 |
Nb | ND | 0.0004 |
Mo | 2.39 | 0.0056 |
Sample ID: INC625 | ||
Component | Result | Stat. error |
Mg | ND | 0.0130 |
Al | 0.201 | 0.0039 |
Si | (0.0044) | 0.0010 |
P | ND | 0.0009 |
S | ND | 0.0018 |
Cl | ND | 0.0003 |
Ti | 0.0741 | 0.0054 |
V | ND | 0.0028 |
Cr | 23.0 | 0.0380 |
Mn | ND | 0.0087 |
Fe | 0.326 | 0.0041 |
Co | ND | 0.0021 |
Ni | 63.1 | 0.0255 |
Cu | 0.304 | 0.0030 |
Zn | 0.0104 | 0.0011 |
Ga | ND | 0.0007 |
Y | ND | 0.0006 |
Nb | 3.50 | 0.0072 |
Mo | 9.44 | 0.0118 |
Sample ID: INC718 | ||
Component | Result | Stat. error |
Mg | ND | 0.0123 |
Al | 0.368 | 0.0040 |
Si | 0.0465 | 0.0010 |
P | ND | 0.0007 |
S | ND | 0.0011 |
Cl | ND | 0.0002 |
Ti | 0.930 | 0.0101 |
V | ND | 0.0035 |
Cr | 20.0 | 0.0293 |
Mn | (0.0638) | 0.0077 |
Fe | 19.5 | 0.0246 |
Co | 0.226 | 0.0054 |
Ni | 50.7 | 0.0242 |
Cu | 0.294 | 0.0029 |
Zn | ND | 0.0088 |
Ga | ND | 0.0006 |
Y | ND | 0.0004 |
Nb | 4.84 | 0.0082 |
Mo | 3.14 | 0.0068 |
ND means the component was not detected; ( ) means the component was below LLQ.
Conclusion
This study illustrates how the NEX DE analyzer yields very good semi-quant results for general screening and monitoring alloy powder composition and mixtures. The Rigaku NEX DE analyzer, with its high performance and simple yet advanced software, provides an easy-to-use and valuable tool for the metal 3D printing industry to ensure proper alloy mixtures and high-quality metal parts.
Related products
NEX DE Series
High-power 60 kV EDXRF systems delivering speed, precision, and small spot measurements
Learn More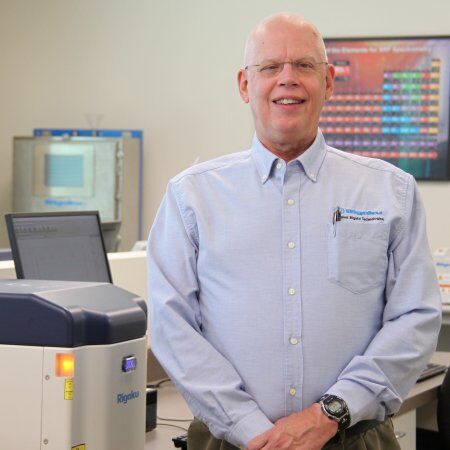
Contact Us
Whether you're interested in getting a quote, want a demo, need technical support, or simply have a question, we're here to help.