Decoding Defects: Failure Analysis Using X-ray CT
1. Introduction to Failure Analysis
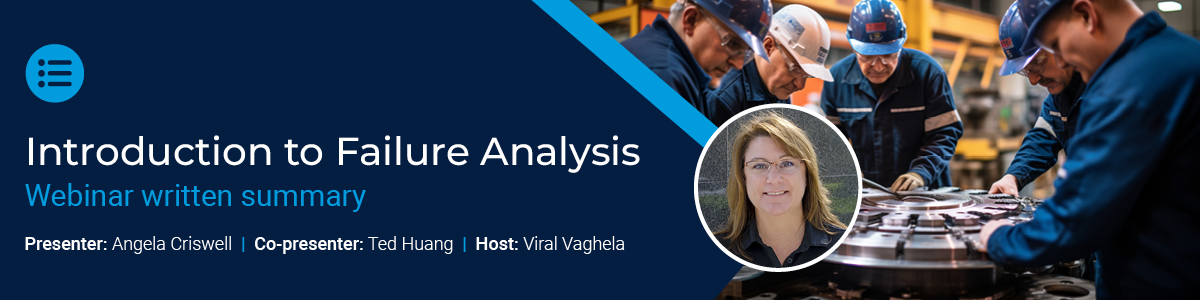
This is a written summary of a live webinar presented on April 24, 2024. The recording and resources are available on the recording page.
Presented by:
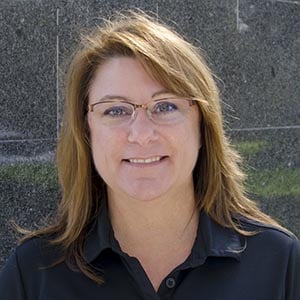
This is a written summary of the webinar Decoding Defects: Failure Analysis Using X-ray CT
1. Introduction to Failure Analysis.
Why failure analysis matters in manufacturing
In manufacturing, keeping products reliable and safe is everything. Failure analysis helps make this possible by figuring out why products fail and finding ways to prevent it from happening again. This process isn’t just about spotting flaws; it’s about understanding the root causes behind them. With these insights, manufacturers can make better products, protect their reputation, and keep consumers safe.
Failure analysis matters at every stage of a product’s life, from design to after it hits the market. When companies run these analyses, they can catch design issues, material weaknesses, and production mistakes early. This proactive approach not only reduces risks but also saves money by cutting down on expensive recalls and repairs.
Common failure analysis techniques
There are destructive and non-destructive analysis techniques. Destructive techniques, as the name suggests, damage or alter the component being tested, making it unusable afterward. A common example is decapsulation in semiconductor analysis, where the outer casing is removed with chemicals, lasers, or mechanical methods to expose internal structures for inspection. Sometimes, the part is also cross-sectioned for closer examination under a microscope. For metals, samples may be machined into specific shapes to conduct fracture, fatigue, or corrosion testing, typically followed by detailed visual and microscopic inspection.
Scanning Electron Microscopy (SEM) is another valuable technique that uses a focused electron beam to analyze surface details. It is generally considered non-destructive when only observing the surface of a relatively small sample. However, when the internal structure is probed using Focused Ion Beam SEM (FIB-SEM) or the sample is too large to fit in an instrument, the sample is damaged. When paired with EDS (Energy Dispersive X-ray Spectroscopy), it can also reveal elemental composition, making SEM widely used in failure analysis.
Destructive techniques
- Decapsulation
- Cross-sectioning
- Fracture and mechanical testing
- Fatigue testing
- Corrosion testing
- SEM, FIB-SEM, TEM (Transmission Electron Microscopy)
In contrast, non-destructive techniques preserve the component for further testing. Basic visual inspection is often the first step, followed by electrical characterization or dye penetrant testing if cracks are suspected. Ultrasonic testing is also popular, using sound waves to detect internal defects like voids without any damage. Imaging techniques like X-ray radiography and X-ray computed tomography (CT) are particularly powerful, allowing for 3D visualization of internal structures and helping identify hidden defects without altering the part.
These methods, especially non-destructive ones, are invaluable in industries that prioritize safety and reliability, as they enable ongoing analysis without compromising the component.
Non-destructive techniques
- Visual/Optical inspection
- Electrical characterization
- Liquid dye penetrant
- Ultrasonic testing
- Acoustic microscopy
- Infrared imaging (IR)
- X-ray radiography
- X-ray CT
In the next section, we’ll look deeper into X-ray CT and its specific uses in different industries.
How X-ray CT supports failure analysis
X-ray CT is a breakthrough tool for failure analysis, allowing us to look inside a product without taking it apart or damaging it. Unlike traditional methods that may involve tearing down the product, X-ray CT allows for a complete look inside while keeping the product intact. This is especially valuable in quality assurance, where protecting high-value components is crucial.
X-ray CT’s detailed 3D images reveal internal defects like voids, cracks, and misalignments that can’t be seen from the outside. By using X-ray CT in quality control, manufacturers can ensure that only top-quality products reach customers.
Non-destructive testing: Changing the game
Non-destructive testing (NDT) has completely changed how failure analysis and quality control are done in manufacturing. Traditional methods often damage samples, limiting further analysis. With NDT techniques like X-ray CT, the product remains undamaged, allowing for multiple inspections and comparison with other tests.
The ability to inspect thoroughly without damaging products is a huge advantage, especially in fields like aerospace, automotive, and batteries, where safety and reliability are essential. NDT finds even the tiniest defects, helping boost safety and performance across complex systems. This approach also efficiently uses resources and supports ongoing improvements based on thorough feedback.
X-ray CT techniques: Applications and benefits
X-ray CT is a flexible tool that is used in sectors like electronics, automotive, and aerospace. One big advantage is its ability to produce high-resolution 3D images, which are key for spotting and analyzing defects that could cause product failures.
In the electronics industry, for instance, X-ray CT can inspect solder joints and find tiny cracks that affect circuit performance. In the automotive industry, it helps examine engine parts to ensure they meet strict safety and quality standards. In the aerospace industry, it checks composite materials for flaws that might weaken the structure. With its ability to reveal internal details, X-ray CT is a go-to tool for ensuring product quality and reliability.
X-ray CT scanner: How to choose the right scanner
When selecting an X-ray CT system, the type of samples you plan to analyze largely determines the system requirements—specifically in terms of X-ray energy and resolution. Since the X-ray source is a significant cost driver, the rest of the instrument’s design, including the stage and detector, is optimized around it. For small samples under 20-30 cm, a compact benchtop system, like Rigaku's CT Lab HX, which operates up to 130 kV, may be ideal. For larger, denser samples, the CT Lab HV system offers higher energy (up to 225 kV), a larger detector, and a large, robust sample stage to accommodate heavy loads.
Resolution also depends on the sample's size and density. Small, low-density samples with fine details require low-energy X-rays and high-resolution imaging, potentially down to submicron levels. Mid-sized, medium-density samples often require adjustable energy settings and resolutions of around 3 microns. Large, dense samples, like engine blocks, need high-energy X-rays for penetration, though ultra-fine resolution may not be necessary. Knowing your sample’s size, density, and required resolution helps you choose the right instrument and set up parameters to collect detailed, accurate X-ray CT data.
To learn more about how to choose the right CT scanner and analysis tools, these blog articles might help:
- How Much Does a Micro CT Scanner Cost?
- How Much Does a Benchtop X-ray CT Scanner Cost?
- X-ray CT Scanner Buyers Guide
- Best CT Analysis Software
- 7 Things to Consider When Buying a Computer for CT Image Processing
Real-world wins with X-ray CT
X-ray CT has played a critical role in failure analysis in several cases.
- Kar, N., "Metallurgical and Mechanical Failure Analysis of an Aftermarket Flywheel," 2021. JotNAFE 37. https://doi.org/10.51501/jotnafe.v37i1.90
- Loveridge, M.J., et al., "Looking Deeper into the Galaxy (Note 7)," 2018. Batteries 4, 3. https://doi.org/10.3390/batteries4010003
For example, it’s been crucial in spotting defects in lithium-ion batteries used in electronics and electric vehicles. By identifying hidden defects that could lead to overheating or even fires, X-ray CT has helped manufacturers address these issues before products reach consumers.
In aerospace, X-ray CT has been used to find micro-cracks in composite materials that wouldn’t have been detectable otherwise. By catching these flaws early, manufacturers could make corrections to improve aircraft safety and performance.
These examples show how X-ray CT not only helps prevent failures but also sparks innovation by providing insights that improve design and production.
What’s next for X-ray CT
The future looks bright for X-ray CT in manufacturing. Advancements like higher-resolution imaging, faster scans, and better data processing are set to make X-ray CT even more effective. On top of that, artificial intelligence and machine learning are likely to make interpreting CT scan data faster and more accurate.
Another exciting development is the trend toward digital twins—virtual models of real-world products. X-ray CT’s detailed 3D models can contribute to creating digital twins, which can help with predictive maintenance and managing a product’s lifecycle. As these technologies advance, X-ray CT will keep playing a key role in ensuring product safety, reliability, and quality, pushing the industry toward smarter, more efficient manufacturing.
What to do next
To learn more about failure analysis and see example investigations using CT, check out the additional resources and watch the original webinar recording here: Decoding Defects: Failure Analysis Using X-ray CT - 1. Introduction to Failure Analysis.
I hope this article helped you see why failure analysis is important and how CT can help. If you are not sure which type of CT scanner is suitable for your failure analysis needs, our team of CT experts can help you figure out the best fit. You can talk to one of our CT experts by clicking the “Talk to an expert” button at the top right of the page or sending us a message at imaging@rigaku.com.
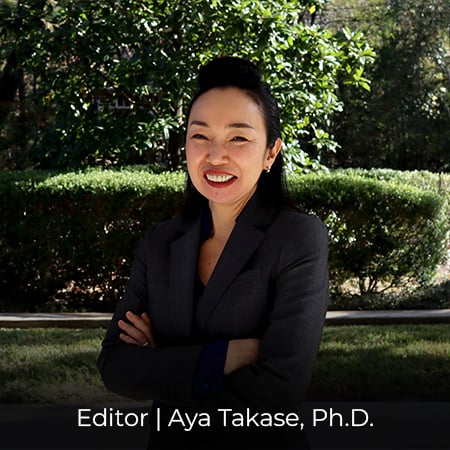
Subscribe to the X-ray CT Email Updates newsletter
Stay up to date with CT news and upcoming events and never miss an opportunity to learn new analysis techniques and improve your skills.
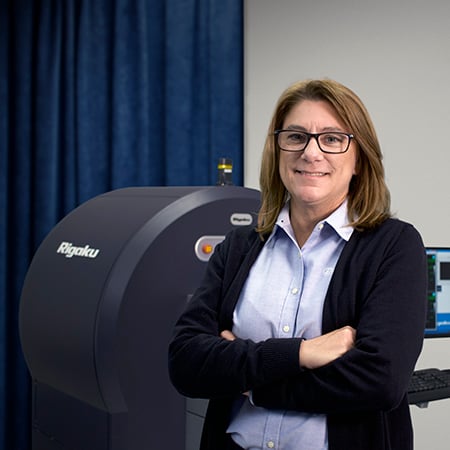
Contact Us
Whether you're interested in getting a quote, want a demo, need technical support, or simply have a question, we're here to help.