Submicron CT for the Pharmaceutical Industry
Introduction
X-ray submicron computed tomography (submicron CT) is one of the most powerful methods for 3D visualization and inspection of any type of sample or product. This non-destructive method provides sufficient resolution and contrast to evaluate any microstructural features, with the ability to resolve structures even below one micron. Moreover, this method requires minimal/no sample preparation, eliminating complicated tasks such as embedding, coating or thin slicing required with other high-resolution methods. The Rigaku nano3DX represents state-of-the-art laboratory-based nanoscale X-ray imaging. This device, when used with deep learning methods, is an unmatched tool for pharmaceutical applications from R&D to production and inspection.
Instrument
The nano3DX is a true X-ray microscope (XRM) with the ability to measure relatively large samples at very high resolution. This is accomplished by using a high-powered rotating anode X-ray source and a high-resolution sCMOS X-ray camera. The rotating anode provides for fast data acquisition and the ability to switch anode materials easily to optimize the data acquisition.
Figure 1: nano3DX particle analysis possibilities.
CT data and results
The microstructure of solid dosage forms of pharmaceutical products is a critical factor that impacts disintegration and dissolution rates. As such, microstructure will also play a key role in bioequivalence and therapeutic equivalence. Being able to image the microstructure of a solid dosage form allows optimization of production and formulation procedures to achieve a robust dissolution response. If an out-of-specification dissolution result is later observed, analysis of the solid dosage form’s internal structure and microstructure can yield a wealth of insights not accessible through traditional analytical approaches, and help resolve mission critical investigations.
New product development can be a highly time-consuming and expensive task. Using Rigaku’s nano3DX, this process can be accelerated, providing immediate feedback on a product’s internal structure when any discrepancies between expected and actual attributes can be identified.
Figure 2: Coating’s morphological analysis–in the internal structure of the analyzed particle, four specific layers were resolvable: core layer, A= immediate drug layer, B= modified drug layer, C= cellulose acetate layer (ordered according to their thickness).
nano3DX provides insight into key factors such as:
Product morphological analysis and
structural analysis
- Coatings – thickness analysis
- Porosity – pores/porous network analysis
- Crystallinity – crystalline phases analysis
- Aggregates detection
- Distribution of API analysis
- Dissolution process evaluation
Optimization of manufacturing process
– Defects Detection
- Cracks
- Coatings thickness homogeneity
- Contamination
Figure 3: Porosity analysis–in the internal structure of the analyzed particle, a high number of pores were detected, which is reflected by the total porosity of 7.43%. Color coding was used according to distance from particle center: Pores in the core layer are yellow and pores in the outer layers are blue.
Figure 4: Coating thickness homogeneity analysis–the thickness of the outer coating layer (cellulose acetate layer) of the analyzed particle varied from 50 to 80 µm, reflecting low manufacturing quality.
Figure 5: Crystallinity analysis–in the internal structure of the analyzed powder, the crystalline phases were resolvable due to high contrast and resolution. The volume of those phases varied from 500 to 1500 µm³.
CT analysis performed by CEITEC – CT Lab
Related products
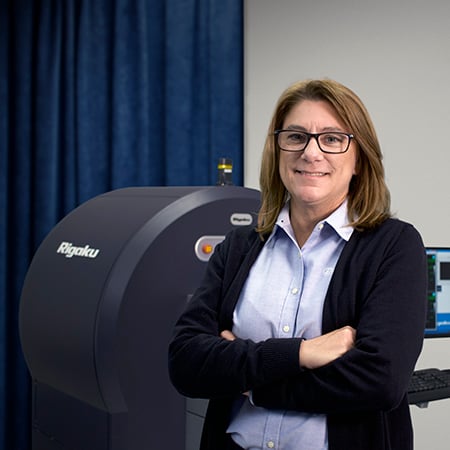
Contact Us
Whether you're interested in getting a quote, want a demo, need technical support, or simply have a question, we're here to help.