Lithium Battery Protection Board Analysis
About the sample: Battery protection board
Lithium-ion battery packs often come assembled with electronics, including a small protection board that protects against short-circuit, overcharge, and over-discharge. These simple protection boards, like the one pictured below, usually include two MOSFETs in series to stop charging when a certain voltage is achieved and to stop discharging when the battery voltage becomes low. These MOSFETs and other electrical components are attached to the board via solder connections. Most solder connections inevitably contain small voids which can affect the reliability of the device.
As a result, it’s common to inspect board solders to characterize the void volume percentage and usually performed using 2D X-ray inspection. X-ray CT (computed tomography) offers the advantage over 2D X-ray inspection because the solder depth and die connection can be fully observed.
Additionally, X-ray CT allows the operator to quantify void volume distribution in solders and better characterize voids that may be obscured in 2D projections because solders and other board components overlap. This example describes data collection for a battery pack, which includes a small protection board and subsequent analysis of MOSFET transistor wiring and solder voids.
Analysis procedure
- In this example, a lithium-ion battery pack containing a small protection board was scanned using a micro-CT scanner, the CT Lab HV.
- CT images were used to inspect the protection board for damage and note areas of interest, including MOSFET transistors.
- Solders were segmented, and a void analysis was performed for several solders. The relative size of each solder was calculated and is shown color-coded versus size, depicted as the voxel count of each solder void.
1. CT scan
The figure below shows a 3D view of the battery pack (left) and the battery pack protection board (center) with an expanded view around one of the two MOSFET transistors (right).
Figure 1
2. MOSFET inspection
3D view and 2D cross-sections of the MOSFET at 90 degrees relative to each other are shown below. The wires and wire connections are clearly visible, with dimensions of ~40 µm and 125 µm, respectively, in the the front view cross-section. The side views show additional dimensions for a thin layer of solder and the board with even smaller thicknesses of ~21 µm and ~32 µm, respectively.
Figure 2
Figure 3
3. Solder inspection and segmentation
Segmentation was performed for solder joints in MOSFETs and capacitors to label voids. Solder void volume was characterized in terms of the number of encompassing voxels. These results are shown color-coded according to size. The figure below shows 2D and 3D views of solder voids in adjacent components of the protection board. Small voids are depicted in red and change to pink, magenta, blue, and green as they increase in volume.
Figure 4
Figure 5 illustrates the advantage of 3D measurement. With X-ray CT, voids can be characterized individually by volume. Additionally, the right-most cross-section image illustrates how X-ray CT allows visualization and characterization of voids that might otherwise overlap in 2D X-ray inspection.
Figure 5
Related products
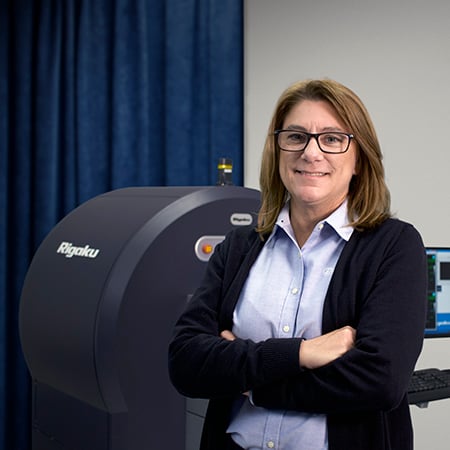
Contact Us
Whether you're interested in getting a quote, want a demo, need technical support, or simply have a question, we're here to help.