Elemental Determination of Whole Coal by the Pressed Powder Method
Introduction
Coal is the most abundant source of energy amongst the remaining fossil fuels in the world. Coal production is classified into two groups based on its usage. Thermal (steam) coal is used for generation of electricity, whereas metallurgical (coking) coal is mainly used for production of steel.
Coal beneficiation (coal cleaning) is critical since it determines the quality of final product. Rapid and accurate elemental determination is therefore important in order to assure that harmful components to the environment such as ash and sulfur are sufficiently low.
X-ray fluorescence (XRF) spectrometry with pressed powder method is a simple analysis technique that can rapidly determine elemental composition of coal with high accuracy and precision. It is therefore well suited for industrial process and quality control. This non-destructive analytical technique has the added benefit of easily being able to determine the concentration of elements that can be lost during ashing process.
This note demonstrates rapid and accurate determination for multiple elements in whole coal by pressed powder method.
Instrument
The Supermini200 is a unique benchtop sequential WDXRF spectrometer with high spectral resolution and high sensitivity for light elements. The spectrometer is designed to minimize installation utilities such as cooling water, special power supply and installation space. For the analysis of light elements, the newly developed sealed proportional detector (S-PC) can be substituted (option) for the conventional flow proportional detector (F-PC). Since the S-PC eliminates the need for an external P-10 (detector) gas cylinder, the Supermini200 can be a truly utility-free WDXRF instrument. It is equipped with an air-cooled 200W X-ray tube and up to three analyzing crystals allowing analysis of element oxygen to uranium.
The functionally versatile software allows easy setup of various types of applications. In particular, the flowbar guides the user step by step for the setting up of quantitative and qualitative analysis conditions.
The user friendly interface of the semi-quantitative analysis program “SQX” allows quick elemental determination of unknown samples without the need for reference materials.
Quant Scatter FP function
”Quant Scatter FP” is a unique function integrated into the Rigaku Fundamental Parameter (FP) software. The function is able to generate dedicated theoretical alphas to correct for matrix effects in empirical calibration curves by the internal standard method using scattering X-rays with arbitrary 2θ angle on continuous X-rays. The internal standard method using scattering X-rays (usually Compton scattering X-ray) without theoretical alphas has been preferred for heavy trace element analysis in some ores because of its ease of use. However, this conventional method does not fully correct for matrix effects especially for ore samples with high heavy element content. Rigaku’s correction scheme overcomes this problem by integrating the scattering X-rays internal standard correction method with theoretical alpha correction by FP method. This advanced correction method for powder samples can cover some lighter elements in coal as well as heavy elements.
”Quant Scatter FP” function (optional) is available for Supermini200 as well as Rigaku Simultix and ZSX Primus family.
Standard and sample preparation
The standard samples used for calibration were commercially available 6 certified reference materials (CRMs) supplied from National Institute of Standards and Technology (NIST), South African producers of Metallurgical and Geological Certified Reference Material (SARM) and U.S. Geological Survey (USGS). The well-dried (2 hours at 105°C) samples were ground together with binding agent (lactose). The ratio of sample to binder is 5 to 1. The sample is then pressed at 200 kN using sample cup. Pressed pellets were covered by polymer thin film (4 μm Prolene® film) for measurement.
Measurement and calibration
Supermini200 was used for measurement of the element lines of Na, Mg, Al, Si, P, S, K, Ca, Ti, V, Cr, Mn, Fe, Ni, Cu, Zn, Sr and Ce. Pd-Kα Compton line and continuous X-rays with a 2θ angle near Cu-Kα were measured for internal standard.
Calibration equation for phosphorous and other elements heavier than sulfur is as follows.
$W_i = (AI_R^2+BI_R+C)\cdot(1+\sum{a_jW_j})$
$I_R = I_i/I_{scat}$
$a_j$: theoretical alpha of element j
$W_j$: weight fraction of element j
$I_i$: intensity of element i line
$I_{scat}$: intensity of scattering line
$A, B, C$ : constant
Results
Calibration accuracies for all components measured in this study are listed in Table 1.
The accuracy of calibration is calculated by following equation.
$Accuracy = \sqrt{ \frac{\sum_i{(C_i-\hat{C}_i)^2}}{n-m} }$
$C_i$: calculated value of standard sample
$\hat{C}_i$: reference value of standard sample
n : number of standard samples.
m: degree of freedom (linear 2, quad. 3)
Calibration curves for Al₂O₃, SiO₂, S, P, CaO and Fe₂O₃ are shown in Figure 1. Trace elements are also calibrated with good accuracy as shown in Figure 2.
Table 1: Accuracy of the calibration curve (unit : mass%)
Element | Concentration range | Typical accuracy of calibration |
Na₂O | 0.018 - 0.29 | 0.019 |
MgO | 0.047 - 0.43 | 0.023 |
Al₂O₃ | 1.0 - 11 | 0.035 |
SiO₂ | 2.5 - 18 | 0.19 |
P | 0.003 - 0.061 | 0.0008 |
S | 0.29 - 1.5 | 0.12 |
K₂O | 0.023 - 0.24 | 0.0031 |
CaO | 0.18 - 1.9 | 0.034 |
TiO₂ | 0.078 - 0.63 | 0.0062 |
V | 0.0012 - 0.0047 | 0.0002 |
Cr | 0.0004 - 0.0067 | 0.0002 |
MnO | 0.0009 - 0.020 | 0.0003 |
Fe₂O₃ | 0.29 - 1.8 | 0.057 |
Ni | 0.0005 - 0.0025 | 0.0001 |
Cu | 0.0006 - 0.0018 | 0.0001 |
Zn | 0.0006 - 0.0048 | 0.0002 |
Sr | 0.0044 - 0.0033 | 0.0003 |
Ce | 0.0006 - 0.0087 | 0.0007 |
Figure 1: Calibration curves of representative components in whole coal. P, CaO and Fe₂O₃ are calibrated with scattering X-ray internal standard and theoretical alpha correction. Blue: Corrected (certified), Yellow: Corrected (uncertified), Circle: Uncorrected
Figure 2: Calibration curves of representative trace components in whole coal. Blue: Corrected (certified), Yellow: Corrected (uncertified), Circle: Uncorrected
Figure 3: Qualitative scan chart of Cl-Kα with Supermini200. The arrow in the figure indicates the 2θ angle of Rh-Lα. Since the Rh-Lα line overlaps with the Cl-Kα line when a Rh target tube is used, a primary filter is necessary for detection of trace amount of chlorine.
Chlorine analysis
Chlorine is undesirable element in coal because it can seriously damage production facilities during the high temperature manufacturing process.
Supermini200 which is equipped with a Pd target X-ray tube has an advantage over Rh target X-ray tubes for the trace detection of Cl. Figure 3 shows that the Cl-Kα peak has no overlap for Supermini200.
On the other hand Rh-Lα originating from Rh target X-ray tubes can interfere with Cl-Kα making it necessary to use a primary filter with inevitably decreases sensitivity.
Chlorine is not calibrated in this study because CRM with reliable chemical values are not available. The lower limit of detection (LLD) of chlorine is estimated from intensity obtained from qualitative scan analysis for one of coal CRMs. The calculated typical LLD of chlorine in coal is 6 ppm at 100 second counting time. It is a significantly low value close to high performance floor standing XRF systems equipped with high power Rh X-ray tube.
Conclusions
This note demonstrates rapid and accurate elemental determination technique for whole coal analysis with Supermini200 and Rigaku advanced correction method for powder samples.
Supermini200 is able to quantify elements important in coal mining. Trace elements as well as ash components can be analyzed in high accuracy. The Pd target X-ray tube allows Cl analysis with high sensitivity since no primary filter is required.
The pressed powder method with Rigaku advanced correction technology is widely applicable for elemental analysis for exploration, mining operation, beneficiation and final product assays.
Related products
Supermini200
Benchtop tube below sequential WDXRF spectrometer analyzes O through U in solids, liquids and powders
Learn More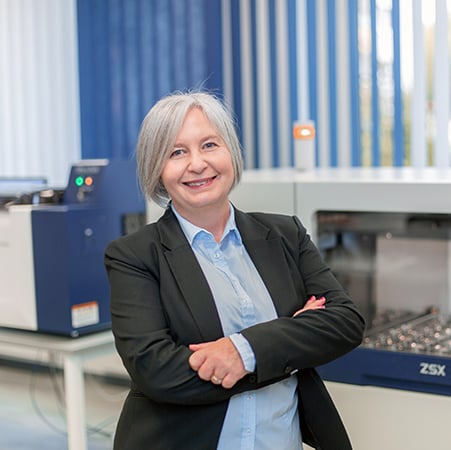
Contact Us
Whether you're interested in getting a quote, want a demo, need technical support, or simply have a question, we're here to help.