Evaluation of Residual Stress of Thin Films by GI-XRD and the Multiple hkl Method
Introduction
Residual stress of thin films has been reported as a cause of cracks and partial expansion of these films, as well as peeling of the films and/or deformation of the substrate, depending on the adhesion strength between the thin film and the substrate. Residual stress X-ray diffraction is one of the methods for evaluating residual stress with high accuracy. The method is, however, difficult to apply to thin films because the X-rays only penetrate the sample surface to a depth of several μm ~ several tens μm, generating insufficient intensity to analyze the X-ray diffraction (XRD) profile. We herein illustrate an example where residual stress of a thin film is evaluated by grazing incidence X-ray diffraction (GI-XRD) for efficiently creating the XRD profile by the multiple hkl method, which uses different Miller indices.
Measurements and results
Figure 1 shows the results of residual stress analysis of an indium tin oxide (ITO) film measured by GI-XRD in which X-rays are widely and shallowly irradiated on the sample surface. To make the angle (ψ) between the specimen surface normal and the lattice plane normal as wide as possible, we used a Cr radiation source. The incident angle was fixed at 1° and 2θ scanning was carried out. The peak positions used as parameters for the calculation of residual stress were obtained from profile fitting. Young's modulus and Poisson's ratio are calculated from the Kröner model, which is applicable to cubic crystals and is close to the experimental value. As a result, compressive stress of -784±74 MPa is observed in the ITO film. The multiple hkl method combined with GI-XRD is a powerful method, as it is an easy-to-use and non-destructive technique for evaluating the residual stress of thin film with high accuracy.
Figure 1: Result of profile fitting (a) and residual stress calculation (b).
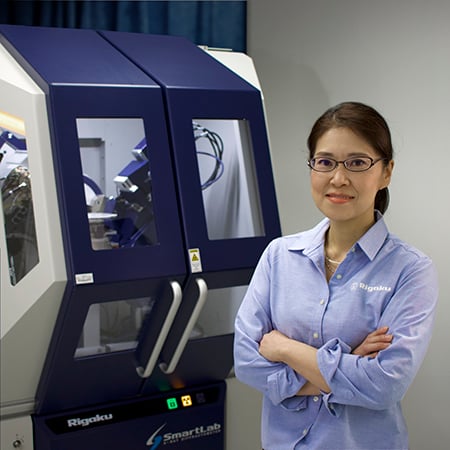
Contact Us
Whether you're interested in getting a quote, want a demo, need technical support, or simply have a question, we're here to help.