Online Sulfur in Heavy Oils
Scope
On-line, real time X-ray Transmission (XRT) measurement of sulfur (S) in heavy or light oils to satisfy the needs of refineries, pipelines, blending operations, bunkering terminals and other storage facilities. Applications include bunker fuel blending to meet MARPOL Annex VI sulfur restrictions, interface detection of different grade fuels delivered via pipelines, refinery feedstock blending and monitoring, diesel/kerosene blending or production, and the quality monitoring of crude at remote collection and storage facilities.
Background
While in-line sulfur gauging - for blending, switching and QC - has been around for years, older technologies never delivered on their promise because those systems did not produce consistent measurements. For the accurate on-line determination of sulfur, the new Rigaku NEX XT resolves those past issues and is thus the perfect tool for blending operations supplying marine bunker fuels and crude feedstock for refineries.
Model: NEX XT
With uniquely engineered hardware and novel proprietary software technologies, the new Rigaku NEX XT system is faster, more sensitive and far more compact than previous generation systems and provides continuous, reliable detection of sulfur from 200 parts-per-million (ppm) to 6.0 wt. %, with analysis times as short as 1 second. The Rigaku NEX XT can operate as a stand-alone analyzer or provide real time closed loop control when tied into a blending or plant wide automation system.
Calibration
Six known field samples with assayed sulfur values were used to establish the crude calibration shown below. Up to 15 product calibrations with 15 standards each can be stored in system memory.
Sample I.D. | Known wt% | Calculated wt% | Deviation | Density | Acq. Time |
1 | 0 | -0.012 | 0.013 | 0.8254 | 60 |
2 | 0.124 | 0.125 | -0.001 | 0.8517 | 60 |
3 | 0.286 | 0.285 | 0.001 | 0.8514 | 60 |
4 | 0.298 | 0.305 | -0.007 | 0.8042 | 60 |
5 | 0.616 | 0.627 | -0.011 | 0.8494 | 60 |
6 | 1.526 | 1.52 | 0.006 | 0.8432 | 60 |
Recovery
To demonstrate measurement recovery, the two lower concentration samples were re-introduced after calibration and analyzed as unknown samples.
Sample I.D. | Known wt% | Calculated wt% | Density | Acq. Time |
2 | 0.124 | 0.128 | 0.8514 | 60 |
3 | 0.286 | 0.285 | 0.8515 | 60 |
Repeatability
To demonstrate instrument repeatability (precision), ten repeat analyses were performed for low, medium, and high crude oils, as static samples, using a 60 sec acquisition time for each measurement.
Sample I.D. | Known wt% | Average wt% | STd. Dev wt% | % Relative |
2 | 0.124 | 0.1234 | 0.0013 | 1.0 |
5 | 0.616 | 0.6134 | 0.0034 | 0.6 |
6 | 1.526 | 1.529 | 0.004 | 0.04 |
Measurement of field samples
Four unknown field samples were measured against the installed calibration and the results are compared to the results measured by the benchtop XRF technique for bulk at-line analysis.
Sample I.D. | XRF wt% | NEX XT wt% | Deviation | Density | Acq. Time |
A | 0.084 | 0.084 | 0 | 0.8003 | 60 |
B | 0.482 | 0.488 | 0.006 | 0.8152 | 60 |
C | 1.85 | 1.89 | 0.04 | 0.8504 | 60 |
D | 0.37 | 0.39 | 0.02 | 0.8149 | 60 |
Analytical stability
The chart below reflects approximately 700 thirty second analysis over a period of 6 hours. The unit reported excellent analytical stability as the observed standard deviation reported was at the theoretical value.
X-ray transmission technique (XRT)
X-ray transmission gauging involves measuring the attenuation of a monochromatic X-ray beam at an energy (21 keV) that is specific to sulfur (S). In practice, a process stream passes through a flow cell where sulfur (S), in the hydrocarbon matrix, absorbs X-rays transmitted between an X-ray source and detector (see schematic at left). The recorded X-ray intensity is negatively correlated to the sulfur concentration; thus the highest sulfur levels transmit the least X-rays.
Transmission of X-rays through the flow cell is given by the following equation:
$T=I/I_0=exp^{(-dt[μ_m(1-C_s)+ μ_sC_s)}$
Where:
I = measured X-ray intensity (after flow cell, in photons/sec)
I₀ = initial X-ray intensity (before flow cell, in photons/sec)
d = density of the hydrocarbon stream
t = thickness of the flow cell path (in cm)
μm = molar absorptivity for the hydrocarbon matrix @ 21 keV (cm²/gm)
μs = molar absorptivity for sulfur @ 21 keV (cm²/gm)
Cs = weight fraction of sulfur (%wt/wt)
An in-line densitometer simultaneously measures oil density and temperature, readings which are automatically incorporated into the sulfur calculation, and output independently for use in process control. An optional water input can be monitored to identify when water content is increasing. A water content of 0.5 wt % may bias sulfur reading 400 – 500 ppm high if not corrected.
Simple, intuitive software interface makes calibration and analysis easy. Calibrate once, and then continuous sulfur results are reported automatically as oil flows through the analysis chamber. The update frequency is user configurable. The system is designed for unattended operation and requires no consumables or routine maintenance. Grab samples can be occasionally taken for verification testing using another technique, such as benchtop EDXRF, and adjustments can be made to the calibration at the system HMI or through a MODBUS® 485 connection.
Sulfur concentration, oil density and temperature, as well as water content (optional) can be output to a DCS or other control systems, giving the operator a complete and real time overview of their product.
Conclusion
XRT gauging has long been an accepted technique for the measurement of sulfur (S) in heavy and light hydrocarbon process streams. Whether used for crude oil blending and monitoring, assaying or blending marine bunker fuels or switching pipelines, the Rigaku NEX XT XRT process analyzer is well suited to meet the varying demands of the industry.
Marine bunker fuel
- Blending operations
- MARPOL ANNEX VI compliance
Pipelines & remote terminals
- Real-time blending operations
- Remote crude collection QC
- Pipeline interface detection
Refineries
- Feedstock blending
- Heavy oil upgrading
- Vacuum resid
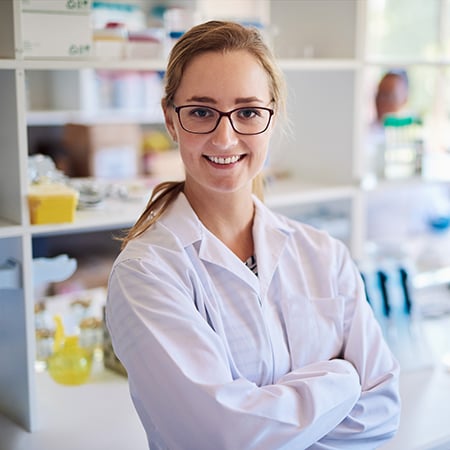
Contact Us
Whether you're interested in getting a quote, want a demo, need technical support, or simply have a question, we're here to help.