Electric Arc Furnace Slag
Scope
The analysis of major oxides iron (Fe), calcium (Ca), and silicon (Si) in electric arc furnace slag (EAFS) is demonstrated for screening purposes, furnace control, and slag quality control. Performance for other oxides is also summarized.
Background
Electric arc furnace steelmaking, also called EAF, typically uses direct reduced iron or ferrous scrap as the feed materials. In the electric arc furnace, lime (calcium) is added to remove silicates and phosphorus. With the addition of oxygen, the ferrous materials are essentially melted, while the remaining material is changed to oxide forms. The slag by-product, also called EAFS, contains relatively constant levels of these oxides and variable amounts of iron, calcium, and silicon oxides. Monitoring the FeO levels indicates the efficiency of the process, while monitoring the ratio of CaO to SiO₂ gives information on the basicity of the slag. The slag is then collected and either refined to be fed back into the steelmaking system, or sold as an aggregate. The high iron, low silicate content, and hardness of the EAFS make it unsuitable as a cement raw material, but make it an excellent aggregate in asphalt and construction usage.
Model: NEX QC+
Calibration
Standards were ground to ~60 mesh. Eleven assayed calibration standards were used to develop empirical calibrations for FeO, CaO, and SiO₂. In this example, the other oxides present did not need to be measured, as their concentrations remained relatively constant and did not cause variations in X-ray absorption properties.
Component | Concentration range (mass%) | Standard error of estimate (SEE) |
FeO | 26.00 – 50.00 | 0.545 |
CaO | 17.74 – 24.41 | 0.251 |
SiO₂ | 12.47 – 14.43 | 0.083 |
Precision
To demonstrate repeatability (precision), the high and low calibration standards were selected and measured in 10 repeat analyses without moving the sample between measurements.
Sample: Standard 681 | ||||
Component | Standard value | Average value | Std. dev | % Relative |
FeO | 49.89 | 49.83 | 0.11 | 0.2 |
CaO | 17.74 | 17.62 | 0.03 | 0.2 |
SiO₂ | 12.47 | 12.40 | 0.02 | 0.2 |
Sample: Standard 624 | ||||
Component | Standard value | Average value | Std. dev | % Relative |
FeO | 25.96 | 25.86 | 0.04 | 0.2 |
CaO | 24.41 | 24.14 | 0.03 | 0.2 |
SiO₂ | 14.43 | 14.34 | 0.01 | 0.1 |
Full characterization
Iron, calcium, and silicon oxides are the main components of interest for optimum furnace control and slag quality. Other oxides may also be measured using NEX QC+. To calibrate, a set of standards that characterizes the particular EAF slag is obtained and assayed for the oxides present. Given a good set of matrix-matched calibration standards that model the slag of interest, the following typical performance can be expected.
Typical Analytical Ranges and Precision |
||
Component | Concentration range | Relative precision (repeatability) |
SiO₂ | 2 – 5% | 0.3 – 0.6% rel |
Total Fe | 0.45 – 0.65% | 0.2 -0.4% rel |
Al₂O₃ | 30 – 40% | 0.3 – 0.6% rel |
CaO | 50 – 60% | 0.1 – 0.2% rel |
TiO₂ | 0.1 – 0.2% | 4 – 9% rel |
MgO | 5 – 8% | 1.7 – 2.2% rel |
Cr₂O₃ | 0.04 – 0.05% | 2 – 5% rel |
MnO | 0.04 – 1.5% | 2 – 4.5% rel |
P₂O₅ | 0.01 – 0.02% | 3 – 8% rel |
S | 0.2 – 0.8% | 0.4 – 1.4% rel |
Conclusion
The NEX QC+ offers technicians and non-technical operators a simple yet powerful and versatile system for quantifying elemental composition using the empirical approach. The results of this study indicate that given stable samples, proper sample handling and proper calibration technique, the Rigaku NEX QC+ EDXRF can achieve excellent results in screening and monitoring the concentration of FeO, CaO and SiO₂ in electric arc furnace slag and other similar matrices. Given suitable calibration standards, other elements and oxides may be measured by EDXRF as well, including MgO, Al₂O₃, TiO₂, Cr₂O₃, MnO, P₂O₅, and S.
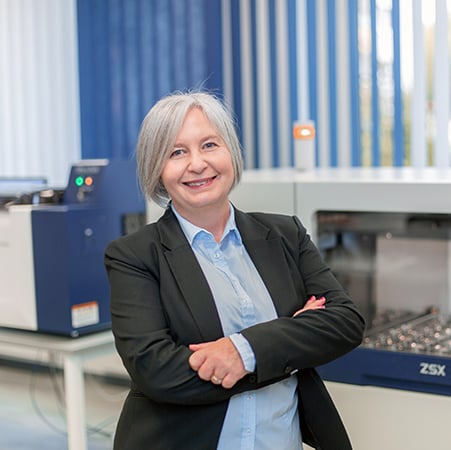
Contact Us
Whether you're interested in getting a quote, want a demo, need technical support, or simply have a question, we're here to help.