Cu Concentrate with Advanced Correction for Fused Beads
Introduction
Global copper supply and consumption has been growing in the past few decades. Copper is one of the important base metals for development of modern nations and it plays a significant role as an essential industrial material for construction, electronics, machinery, transportation and so on.
Copper ore and copper concentrate, which are mainly sulfide, contain a variety of minor elements, which are valuable elements as byproducts, or harmful to quality in copper metal products and hazardous to environment and human health. Therefore, rapid and accurate determination of various metals of major and trace amount in copper ore and concentrate is important for process control in the beneficiation and smelting of copper.
X-ray fluorescence spectrometry is the best analysis method to monitor ore grade and impurity with high precision, accuracy and rapidity.
The fusion method is an effective sample preparation technique for accurate analysis of a wide variety of powder samples including minerals and ores by XRF spectrometry since it eliminates heterogeneity due to grain size effects and mineralogical composition. In order to take advantage of the fusion method, however, appropriate corrections for errors arising from fusion processes are required. Possible errors in the fusion process are weighing inaccuracies, loss on ignition (LOI), gain on ignition (GOI), decomposition of oxidizing agent and evaporation of flux.
This application note will introduce an advanced correction technique for fusion method and application for copper concentrate analysis.
Instrument
The ZSX Primus III+ is a floor-standing sequential wavelength dispersive X-ray fluorescence (WDXRF) spectrometer, which has advantages of high spectral resolution and high sensitivity for light elements. The instrument is designed to provide reliable analysis results and its flexibility provides multi purpose availability to a wide range of applications.
The ZSX Primus III+ is equipped with a 3 kW Rh target X-ray tube. Analyzing crystals (up to 10 crystals) can cover from beryllium to uranium.
The instrument also has a built-in intelligent auto sample changer (ASC). The ASC is upgradable to 48 samples for high demand applications and processes. The ZSX Primus III+ has a unique optical configuration designed to minimize errors caused by uneven bead surface. Therefore, it is possible to perform high precision and accurate analysis of fused beads in which the surface becomes curved with deformation of platinum crucibles from continuous fusion operation. The software is further improved regarding easy-to-use operation for users who are not experienced. In particular, the flowbar system fully supports operation for the setting-up of quantitative analysis.
The operation software provides users with high flexibility and availability for various applications. Built-in FP program is expanded to generate appropriate theoretical alphas even if large GOI occurs in the sample during fusion so that the total LOI value becomes negative. As an advanced expansion, the program can generate coefficients to correct for variation of weight ratios of flux and oxidizing agent to sample due to approximate weighing.
Sample preparation
Twelve certified reference materials of copper ores and concentrates were used as references for calibration. In the fusion process of sulfide minerals, it is required to prevent the Pt crucible from being damaged by sulfides and metal components during fusion. Then, before fusion by the fusion machine, calcination with oxidizing agent was performed to complete oxidization of sulfides and metal components in the sample. The procedure of fusion is as follows.
The well-dried (2 hours at 105°C) sample and 12-22 flux were weighed out 0.200 g and 4.000 g, respectively. The sample and flux were mixed well in a Pt crucible. Then, 0.9 mL of 20 % solution of LiNO₃ and about 2 mL of pure water were added as oxidizing agent. The mixture was calcined in an electric furnace at 800 °C for 10 minutes. After cooling, 20 μL of 10 % solution of LiBr was added as releasing agent and then fused at 1050°C in the fusion machine.
Calibration and results
Measurement was performed for the elements of Pb, As, Zn, Cu, Co, Fe, Mn, Ti, Ca, K, S, P, Si, Al, Mg and Na by using the ZSX Primus III+. In the calibration, all of these elements were treated as oxides. Matrix correction coefficients (alphas) applied to the matrix correction in the calibration were theoretically calculated by built-in fundamental parameter (FP) software.
A calibration formula[1] to correct errors in the fused beads used in this analysis is as follows:
$C_i = (bI_i + c)(1+\sum^{j \neq L}{\alpha_j C_j + K + \alpha_F R_F + \alpha_X R_X})$
$C_i$: concentration of element i
$C_j$: concentration of element j
$I_i$: intensity of element i
$α$: matrix correction coefficient
$R_F$: flux ratio
$R_X$: oxidizing agent ratio
$L$: balanced component, LOI
$b, c, K$: constant
The summation term in the formula is alpha correction term for absorption and enhancement effects, which also eliminates the errors caused by LOI/GOI effects. The latter two terms in the parentheses are flux ratio and oxidizing agent ratio correction term, respectively. There are two correction models in which the definitions of flux ratio are different. One is flux weight model in which the flux ratio RF is weight ratio of flux to sample. The other is bead weight model. The bead weight model, which uses (Bead / Sample -1) as the flux ratio RF, can also correct for the error due to flux evaporation in addition to other error factors.
In this note, calibrations are demonstrated using bead weight model.
Figure 1 shows calibration curves for representative components in copper ore. Typical accuracy of calibration, expressed as elemental concentration, of the representative components in Figure 1 are shown in Table 1.
Figure 1: Calibration curves of representative components in copper ore and concentrate. Open circle: uncorrected point; Solid diamond: corrected point
Table 1: Typical accuracy of calibration for representative elements (unit: mass%, *: ppm )
Element | Typical accuracy of calibration | Calibration range |
Cu | 0.16 | 0.144-23.8 |
Zn | 0.061 | 0.001-12.4 |
Pb | 0.010 | 0.016-1.30 |
As* | 29 | 52-1280 |
Fe | 0.20 | 1.57-25.4 |
S | 0.097 | 1.23-29.8 |
All values are expressed as elemental concentration
The accuracy of calibration is calculated by the following formula:
$Accuracy = \sqrt{ \frac{\sum_i{(C_i-\hat{C}_i)^2}}{n-m} }$
$C_i$: calculated value of standard sample
$\hat{C}_i$: reference value of standard sample
n : number of standard samples.
m: degree of freedom (linear 2, quad. 3)
Verification of the correction method
Availability of the correction method was examined by a test bead of one copper concentrate selected from the certified reference materials. The test bead was prepared with intentional variations of weighing of sample, flux and oxidizing agent.
Table 2 shows analysis results of the test bead for representative components. The analysis results are consistent with certified values. The result indicates that this method is effective to correct possible multiple errors in the fused bead analysis.
Table 2: Analysis result of test bead (unit: mass%, * : ppm )
Element | XRF result | Certified value |
Cu | 23.87 | 23.79 |
Zn | 1.21 | 1.19 |
Pb | 0.339 | 0.333 |
As* | 840 | 795 |
Fe | 24.8 | 24.7 |
S | 28.1 | 27.6 |
All values are expressed as elemental concentration
Conclusions
The fusion method with improved correction for errors due to making beads by expanded FP program was successfully demonstrated in the copper concentrate analysis. This correction method is convenient and an easy-to-use universal technique available for various errors in the fusion method. It is also a unique method to correct complicated sample weight variation in the fusion such as LOI and GOI occurring simultaneously as well as sample and flux weighing inaccuracy. The high versatility described above provides accurate results for various applications of powder sample with fusion method.
Reference
[1] Homma, H., Inoue, H., Feeney, M., Oelofse, L. and Kataoka, Y., Adv. X-ray Anal., 55 (2012).
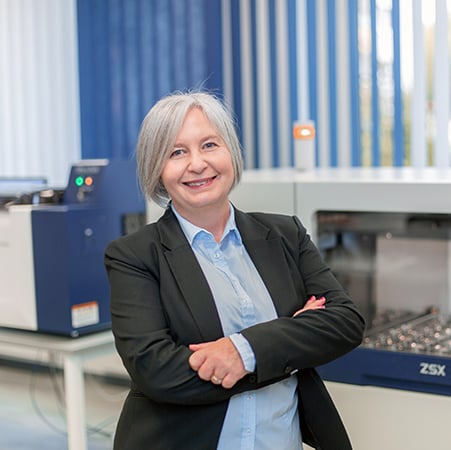
Contact Us
Whether you're interested in getting a quote, want a demo, need technical support, or simply have a question, we're here to help.